3 Reasons to Use Computerized Cutting for Plastic Products
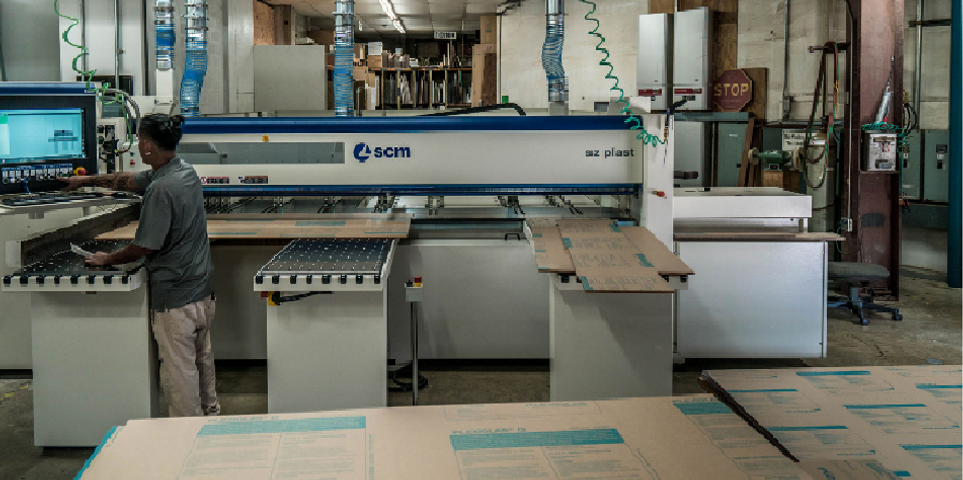
If your business uses plastic components, you should partner with a company that offers computerized cutting. Using a computerized system benefits plastic products manufacturing and your bottom line in the following ways.
3 Reasons to Cut Plastic Products With a Computerized System
1. Fewer Errors
If you rely on plastic components for your construction company, an error in a batch could slow your operations to a halt, wasting time and money. This is particularly a problem when relying on a manual method, which always has the risk of human error. A Computer Numerical Control (CNC) router takes out the guesswork. It uses a digital design file to guide the spindle producing the plastic. Even intricate shapes and designs can be made without increasing the risk of errors.
2. Efficiency
Because a CNC router doesn’t depend on human input for each piece, it can quickly turn out a batch of plastics cut to the specified size. Its spindle runs at more than 30,000 rpm for efficient, clean cuts. You then receive your products promptly and can use them in a project or pass them on to your customer.
3. Less Waste
The force behind CNC routers is computer-aided design software, which allows for detailed layouts of the object being cut. Not only is it easier for you to design your products, but you’ll also spend less money on prototypes. When you have a final design, the precision of a CNC router generates less wasted material, reducing overall costs.
If your contracting team, restaurant, or marine business needs a reliable source for plastic products, turn to Min Plastics & Supply. For more than 60 years, they’ve served the plastic needs of businesses throughout Hawaii from their base in Honolulu. Their wide inventory of plastic materials includes acrylic, polycarbonate, HDPE, and PVC. To start planning your project, call (808) 847-1511 or visit their website.
About the Business
Have a question? Ask the experts!
Send your question