What You Should Know About Thermoforming
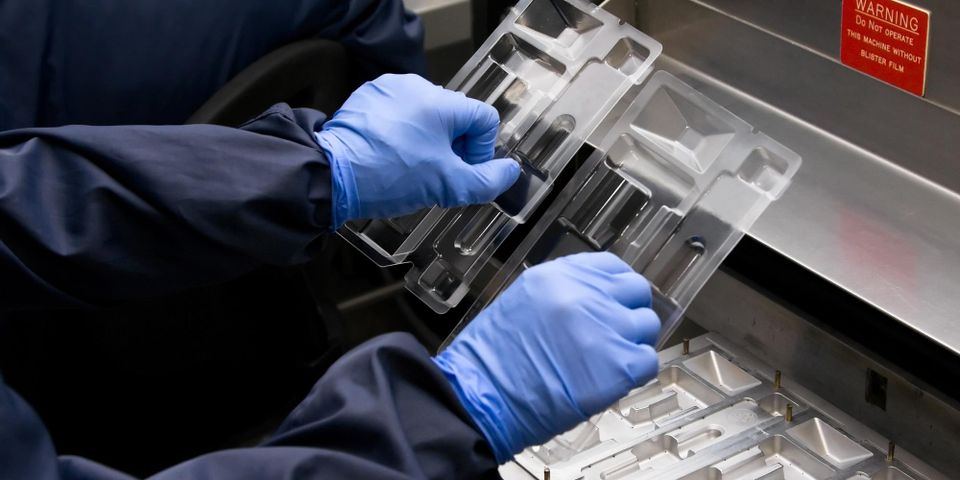
In the industry of custom fabrication, thermoforming has emerged as especially useful and popular. The more you know about this process of shaping plastic products, the better you’ll be able to take advantage of it for your own manufacturing needs, so consult the breakdown below.
What Is Thermoforming?
The process of thermoforming involves combining heat and pressure to make a piece of plastic malleable. The plastic is then cooled in the shape of a mold to create the specified product. While a customer is welcome to provide their own mold if they have one, suppliers can create one on the spot.
What Is It Used For?
Thermoforming is especially handy when you need to customize a plastic product. It can be used to create everything from new skylights—molded to the exact shape you need for your roof—to packaging for a set of tools. The process offers a unique product tailored to your needs that can’t be bought in a store.
What Are Its Benefits?
Beyond the flexibility in use, thermoforming has many other benefits. It’s relatively inexpensive since all types of plastic are affordable base materials. Suppliers can also produce plastic goods extremely quickly, so it’s easy to meet a tight production cycle. Plus, you can choose from design-related extras like color options.
The next time you need high-quality plastic products in Hawaii, get in touch with Min Plastics & Supply in Honolulu. In business for over 60 years and a member of the International Association of Plastic Distributors, the family-run business will use thermoforming to outfit you with the exact plastic shape you need. Place an order for plastic products by calling (808) 847-1511 today, or learn more about the company’s offerings by visiting their website. You can also find reviews from satisfied previous customers on their Yelp page.
About the Business
Have a question? Ask the experts!
Send your question