Stopping Recurring Malfunctions: Insights From Your Local Machine Shop
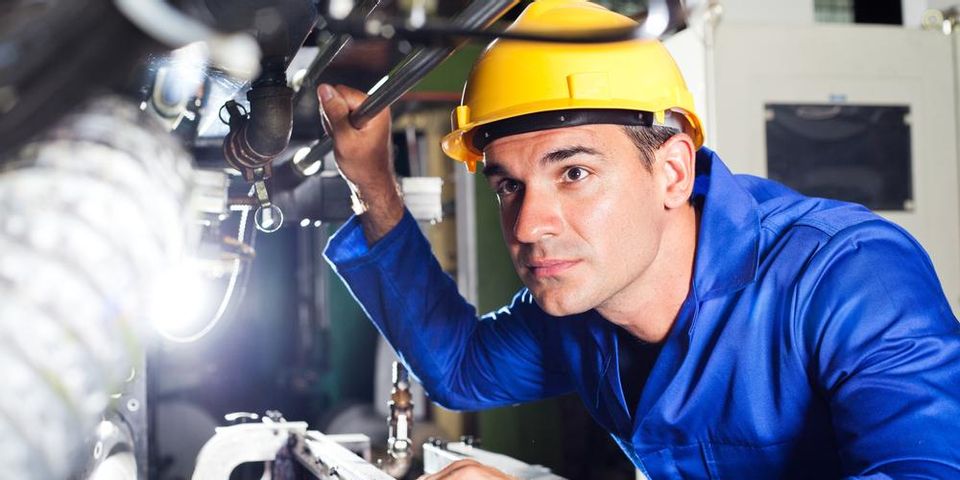
Every time you halt operations to repair machinery, it costs your company money. Although standard wear and tear are going to call for minor repairs on occasion, you should not have to address the same issue over and over. When a particular piece of equipment has a recurring malfunction, you can only halt operations so many times before wondering if replacing it makes fiscal sense. Since replacing machinery is a major investment, it’s wise to approach troubleshooting from all possible angles before deeming malfunctioning equipment useless. Here, the knowledgeable technicians at R. A. Heller Co., a leading machine shop in Cincinnati, share a few common causes of recurring issues.
7 Factors That Could Be Contributing to Recurring Machine Failure
1. Overlooking Certain Parts
Even the simplest pieces of equipment can be comprised of hundreds of moving parts. With so many of them out of sight, it’s easy to overlook those in need of cleaning or lubrication. Failing to tend to certain parts every time you perform routine maintenance can cause the same recurring malfunctions.
2. Missing the Underlying Problem
It’s entirely possible for a piece of machinery to have multiple problems at any given moment. If you fix one issue but fail to address the others, the same operating failures will inevitably occur repeatedly.
3. Ignoring Faulty Wiring
If a loose, damaged, or dirty connection is responsible for the malfunction, reconnecting the wires will repair it—temporarily. Until you replace the wiring entirely, though, you can expect the connection to keep wavering.
4. Pushing the Machine Too Hard
A machine that runs at full capacity 24 hours a day is naturally going to require more maintenance than one running at half its capacity all the time or at full capacity for just 12 hours a day. Every piece of equipment has weak points and pushing it too hard will reveal them. If the same problem keeps happening, it could simply be a result of excessive wear and tear. No matter how many times you address the issue, it will keep arising as long as you run the machine harder than you should.
5. Ignoring Warning Signs
When equipment is overdue for maintenance, there will be various signs. It might not run as efficiently, for example, or it may be much louder than normal. Ignoring these signs is going to cause malfunctions—the same ones that arise every time you ignore them.
6. Failing to Align or Calibrate
A reputable machine shop should explain which pieces of equipment need to be calibrated before every new job, and which need to be realigned periodically. Failure to perform either critical step will force the machine to compensate, which will wear down the same components and result in the same malfunction every time this particular oversight occurs.
7. Letting Debris Accumulate
Dust, dirt, and other debris can damage more sensitive components. To prevent these sensitive parts from breaking down periodically, clean and lubricate the equipment regularly.
If your equipment keeps failing, turn to R. A. Heller Co. Based in Cincinnati, this 20,000-square-foot machine shop can handle repair jobs of any size. Services include piston rod repair, precision grinding, and hard chrome plating. Since 1946, they have been providing quality equipment that’s built to last for clients in various industries. Locally owned and operated, they value each and every client—some of whom have been turning to them for 60 years—and will strive to exceed your expectations, too. Visit their website to learn more about the industries they support or call (513) 771-6100 to discuss your needs today.
About the Business
Have a question? Ask the experts!
Send your question