5 Common Linear Bearing Mistakes That New Factory Owners Should Know
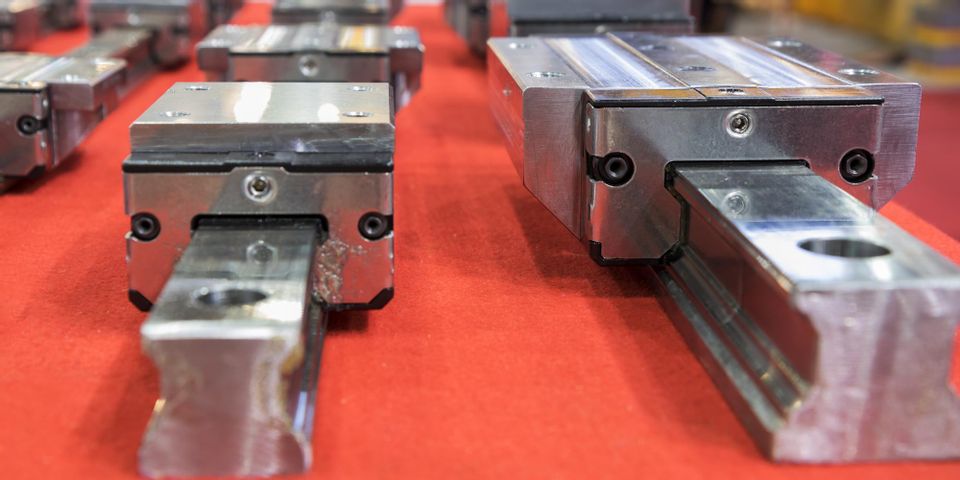
If you’re in the process of setting up a new factory, linear bearings are one important component you’ll need to consider. Comprised of a moveable unit attached to a guide rail, these machining systems allow for free linear movement. When the right solutions are installed, these bearings can help deliver smooth production capabilities. But if mistakes are made during setup, you may find that your equipment isn’t running efficiently, faces premature wear, or provides stick operation.
Linear Bearing Mistakes That Could Complicate Factory Operations
1. Misaligned Mounting
Properly mounted linear bearings will be straight and parallel to other tracks. They should also be mounted level with a flat surface. If the rails are misaligned, not parallel, or uneven against the surface, you may experience a variety of problems—such as reduced load capacity, speed limitations, premature wear due to increased friction, and vibrations.
2. Not Considering the Coating
Linear bearings are typically crafted from hard metals—such as carbon or martensitic steel. While this hardness is preferable in terms of durability, these metals tend to be vulnerable to corrosion when exposed to moisture. Fortunately, you can prevent this problem by coating your linear bearings with hard chrome plating—a rust-resistant shield.
3. Selecting the Wrong Rail Shape
Whether you choose a round or square rail will ultimately depend on the machining calculations you make. However, round rails are generally favored for their ability to span gaps, provide smoother movement, and lower cost. Compared to square rails, round models also are more forgiving when alignment issues cannot be avoided. But if you need improved accuracy under heavy loads, square rails tend to be the most preferred—especially for milling and precision grinding applications.
4. Incorrect Spacing
If rails shake when moving in either direction, they may not be spaced out appropriately according to their load and may need more distance between them. In general, manufacturers should follow a 2:1 rule in which for every inch between bearings, the payload’s center of gravity should not exceed two inches from the rail.
5. Not Testing Performance
After installing, replacing, adjusting, or repairing linear bearings, it’s crucial to test the system’s entire run. During the test, you should be able to pinpoint and fix issues that impact the speed, load capacity, or friction of the bearings.
When you’re searching for machined supplies to support your factory operations, R. A. Heller Co. has the resources you need. Serving Cincinnati, OH, manufacturers for more than 70 years, this machine shop is recognized for providing custom systems and parts—such as linear bearings—that provide precision and durability. Well-versed in machining specs, these specialists can also help you select solutions that fit the needs of your factory. And, if corrosion is a concern, they are equipped to provide high-quality hard chrome plating to protect your hardware. Visit this shop online or call (513) 771-6100 to learn more about their products and services.
About the Business
Have a question? Ask the experts!
Send your question