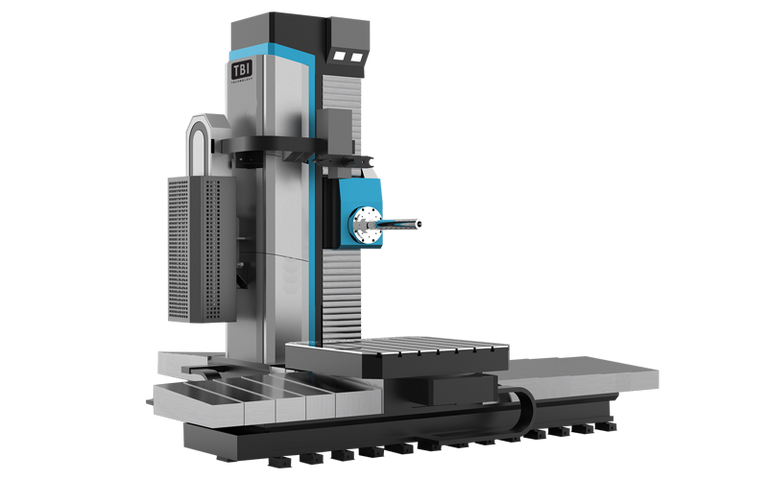
Boring mills are a staple of machining equipment that serves the purpose of widening cylindrical holes in materials. Today’s equipment is prized for its ability to produce smooth interiors and deliver consistent shaping—even when it's used on large and hefty objects. But it took a few hundred years for these tools to get to the level where they are now. To showcase how far the boring mill has come, here’s a brief look at this manufacturing tool’s evolution throughout history.
Consistent Cylinders
Prior to the 1770s, boring was often a rudimentary process that involved casting a cavity in the object—such as the barrel of a cannon—and reworking the imperfections out inside the hole with a manual bore. Other techniques included using a cantilevered borer or simply hammering a cylinder out of iron.
This direction changed in 1775 when inventor John Wilkinson patented the first horizontal boring mill. His device placed the cylinder on a horizontal shaft and relied on a gear-driven cutting tool that was supported on both ends of the shaft. This double-sided support was a major advance from the single-sided capabilities of the cantilevered borer.
Wilkinson’s invention played a major force in the Industrial Revolution, as it was used to bore uniform cylinders for steam engines. This consistent shaping allowed the engine to run more efficiently.
New Directions
Up until the 1880s, industries were used to boring horizontally. But in 1883, a man named E.P. Bullard turned the concept on its head by using a vertical shaft to bore into materials in an up-and-down fashion.
Eventually, this would lead to the vertical turret lathe, which has maintained a long history as a dependable oil drill. Manufacturers continued to improve upon horizontal and vertical boring mills by adding new attachments to create larger cylinders.
Computer Precision
The 1950s introduced CNC—or computer numerical control—boring mill technology. The early versions of these machining tools utilized a series of codes to automate different aspects of the boring process—such as feed rates and positioning. These codes were “programmed” into the machine by way of a punch card.
As computer technology advanced, boring mills gained greater precision, speed, and handling abilities. These systems integrated with computer-aided design software, allowing manufacturers to reproduce 3D designs directly from the program to the physical cylinder.
Specializing in machining, R.A. Heller Co. is known for producing a wide range of custom solutions for various industries. Based in Cincinnati, OH, this machine shop offers precision grinding, horizontal boring mill capabilities, piston rod repairs, and hard chrome plating. To learn more about how this team can create or refine the unique parts you need, visit their website or call (513) 771-6100.
About the Business
Have a question? Ask the experts!
Send your question