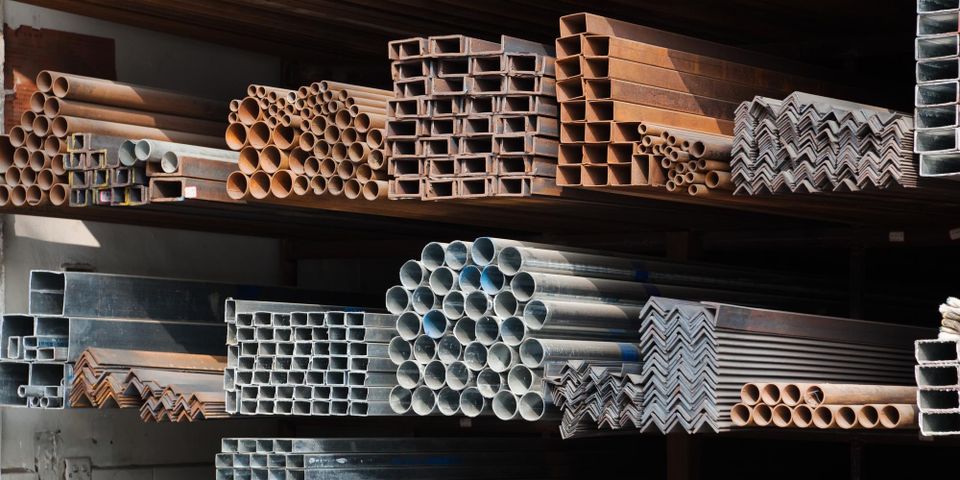
Internal grinding is the process of fashioning bores and holes in commercial materials. It’s a complex process that demands precision so machined parts function correctly. Below is a helpful guide on the topic so you can determine if you need this service and the next steps to take.
How Do Internal Grinders Work?
Internal grinding relies on a large selection of grinding wheels. These are attached to a grinding machine. The rotary devices are operated manually or by programming numerical instructions into an automated CNC machine.
When the grinding wheel spins rapidly—roughly 6,000 sfpm—in order to grind the bore of the particular part. Internal grinding is performed either vertically or horizontally, depending on the length of the material and size of the grinder.
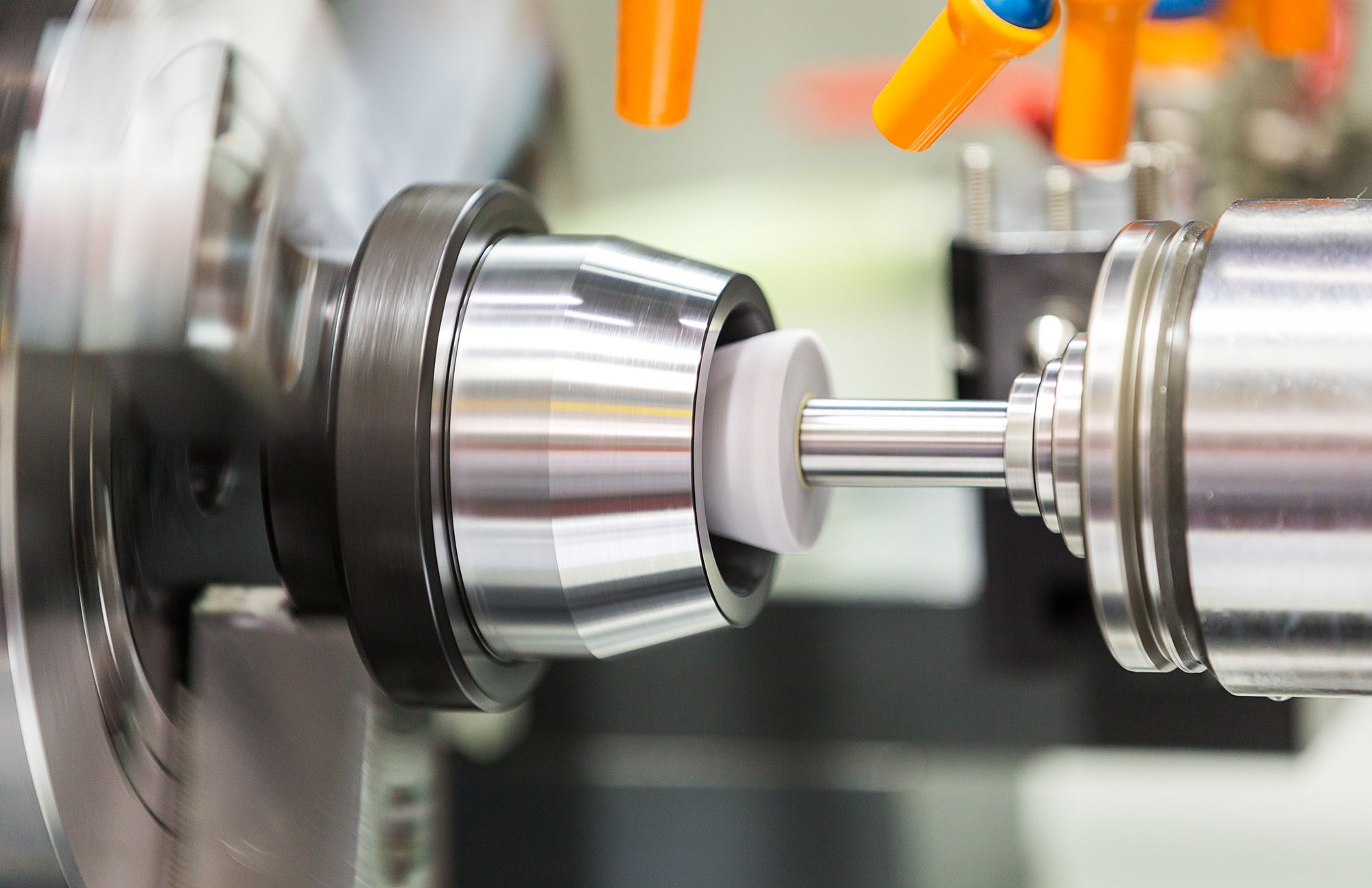
There is a large selection of grinding wheels. They come in various shapes, including wide, narrow wheels for large, shallow holes and long, thin, tapered heads to reach into the bore. Aluminum Oxide wheels are most commonly used.
These are typically 60% to 80% of the diameter of the hole. The abrasiveness of the wheel affects how fine the finish is. A 10 to 24 rating is the roughest. This is recommended for a fast removal rate. A piece of steel alloy or cast iron may then be ground by a wheel to achieve various finish requirements.
How Are They Used?
Internal grinding is used to grind many parts. Bushings, Sleeves, and Housings are common parts to be ground. They’re common in all types of industrial machinery.
Residents of Cincinnati, OH, turn to R.A. Heller Co. for their internal grinding needs. These professionals have served the area since 1946 and employ expert machinists in their 20,000 sq. ft. machine shop. Visit their website to learn about their hard chrome plating, grinding, and hydraulic repair services. You’ll find more insights on their Facebook page or can call (513) 771-6100 to speak with a representative.
About the Business
Have a question? Ask the experts!
Send your question