How to Lubricate Industrial Bearings
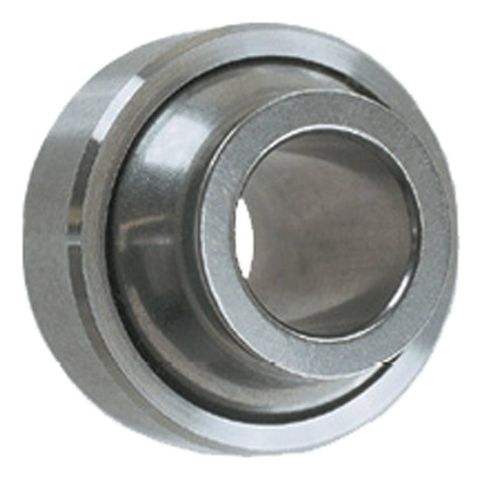
In a material handling and conveying system, bearings ensure belts and chains run smoothly. These essential parts are designed for maximum durability. Bearings that aren’t sealed for life must be lubricated on a regular basis to maximize life. If you maintain an agricultural or industrial plant or piece of equipment, here’s what to consider when lubricating bearings.
Why Some Bearings Need Lubrication
While some products come pre-sealed or filled, others require periodic lubrication. Lubricant prevents excessive contact between metal parts, absorbing friction that can cause damage. Without it, the bearing may yield under the pressure and heat, failing prematurely and bringing your manufacturing processes to a halt.
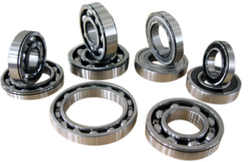
Bearings with ample lubrication are more resistant to corrosion and damage caused by metal flakes, dust, and other airborne contaminants. Even minimal corrosion inside the bearing decrease life by increasing drag and causing misalignments, then failure of your material handling and conveying equipment.
Best Practices for Lubricating Bearings
Your preventative maintenance program (PM) and the correct grease determines how long bearings last in your application. Industrial grease is typically composed of approximately 85% base oil, with the remainder made up of soap or another thickening agent. The U.S. National Lubricating Grease Institute (NLGI) classifies greases according to their stiffness, with ratings ranging from 000 (soft) to 6 (stiff). Most industrial applications require products between NLGI Class 1 and 3.
Using improper lubricants will reduce the life of your bearings. Manufacturers recommend different stiffness based on the amount of vibration and heat that your equipment experiences, however #2 grease works well for most bearings. Load conditions and the size of the bearing also matter for lubrication amounts and frequency. Check your manufacturer’s manual for details about what lubricant to use and when. Speed and hours in service each week, as well as, shock loads, (service factors) determine how often to (PM) your bearings. Its extremely important not to over-grease your bearings too. A general rule of thumb, is 1-2 pumps of grease/inch of shaft diameter, ideally, it should be applied while the shaft turns slowly. Always turn the shaft before adding additional. Many new bearings are pre-lubricated at the factory and can just be installed, check with the manufacturers instructions before adding grease.
To prevent contamination, apply grease as the very last step when replacing a bearing. When lubricating, always leave up to 30-50% free space in the housing to allow excess grease to seep out when you start the machine. As a final solution to lubrication maintenance, consider a lube free option like, Cobra Solid Lube from Unique Technologies, in New Jersey. Go to; utausa.com, or IPTCI Bearings IP69K waterproof and dustproof maintenance free offering. Go to; IPTCI.com
If you need to replace damaged bearings, turn to Industrial Component Sales, Inc. of Hudson, WI. With offices in Bemidji, MN, and Southern, WI, the Representatives for PTI/-IPTCI Bearings. They have provided parts for material handling and conveying machinery for over 20 years. They work with only the finest manufacturers in the industry, including P.T. International®/ IPTCI Bearings and of course QA1®. Visit their website for more on their line of products, or call (612) 991-0263 to get in touch with their headquarters in Hudson.
About the Business
Have a question? Ask the experts!
Send your question