A Guide to Roller Chains
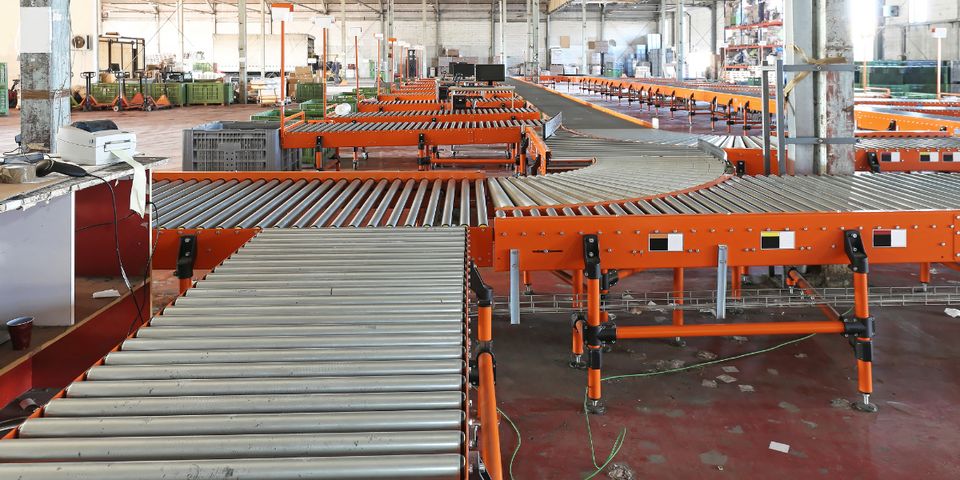
A motion control system allows the transport of a load by using a motor to convert electrical energy into mechanical energy. However, a system may require roller chains connecting to the motor's output shaft and the machine's conveyor head shaft. Although farm owners often see roller chains in agricultural machines like hay bale conveyors and harvesters, they always recognize the importance of replacing them annually to keep the machines working. Use this guide to learn more about the product and keep it in good condition.
What Are Roller Chains?
Although many names contributed to the roller chain's design, it wasn't until 1880 when Hans Renold invented the bush roller chain that its purpose became widely known in industrial and agricultural machinery. It is a series of cylindrical rollers that connect through links forming a typical chain link structure. The rotating sprocket of the motor and the machine's sprocket are attached to one end of the roller link to enable either slow or quick motions.
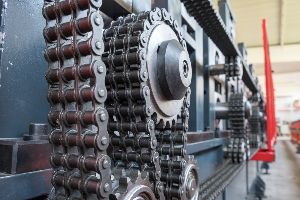
A sprocket using sturdy teeth allows stable movement by continually engaging the chain and turning. Although it uses the same mechanism, the roller chains used in manufacturing, agriculture and industrial differ in styles and size. To find chain size, it is common to measure the distance of the sprocket's teeth using calipers to determine what size Chain Pitch you need for your machinery. you will also need to know, side plate height, pin length to help put the correct chain in your application.
How to Maintain Roller Chains
- Proper Lubrication: Use non-detergent petroleum-based oil for lubrication. 30 weight is always a good choice. If possible, use a brush to assure penetration between the roller, pin and bushings. This helps protect the metal from moisture and dust, which can lead to corrosion.
- Regular Inspection: Clean the product to eliminate debris, then look for signs of wear and tear. Look for shiny and misshapen components to determine misalignment or overload. If any parts are deformed or broken, replace the entire chain to avoid unnecessary strain on the drive. Tension is critical, a general rule is; 1/2 inch or less in slack between the sprockets, but overtensioning can be just as detrimental.
- Professional Maintenance: To prevent machinery failure, schedule expert maintenance every 6 (depending on usage). A qualified technician can detect anomalies that can keep you from unexpected failures. Don't forget to change your sprockets, they are an integral part of chain life.
If you need high-quality roller chains for your business, contact Industrial Component Sales Inc. in Madison and Hudson, WI, as well as Bemidji, MN. With 40 years of industrial sales experience, this team has provided reliable and trustworthy roller chain solutions from Maxco/HKK chain and sprocket company www.maxcochain.com. In addition, they have a solid selection of products such as sprockets, rod ends, belts and sheaves to offer. Call (651) 270-0151 to speak with a team member, and visit the website to learn more about their products.
About the Business
Have a question? Ask the experts!
Send your question