An Ounce of Prevention – The Value of Association Common Area Preventative Maintenance
By HMI
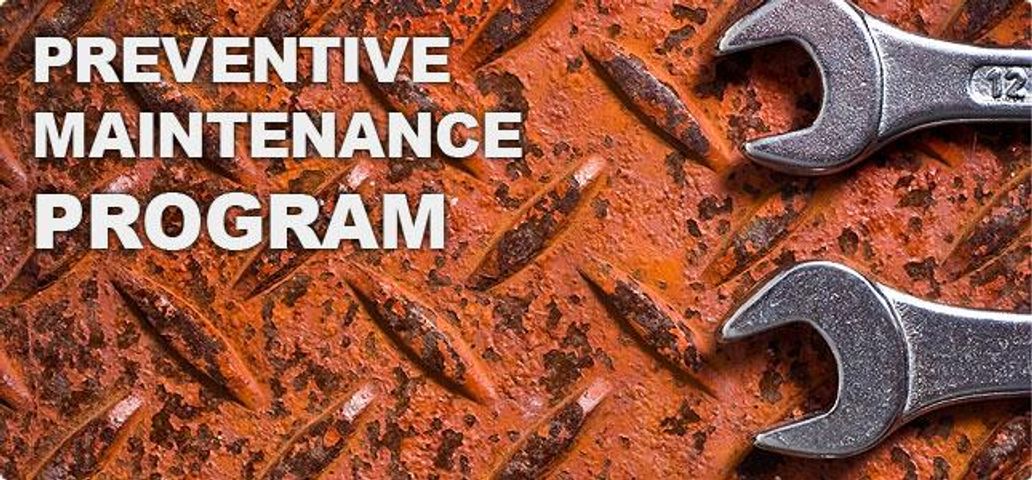
There is a very old and time-tested proverb: An ounce of prevention is worth a pound of cure.
Nowhere is this more true than when it comes to preventive maintenance for common area elements for a homeowner or condominium association. Stating the obvious, materials utilized in the construction of common area equipment and structures age over time. With a strategy based on basic preventive maintenance, it becomes possible to extend the useful life of these common elements.
In fact, the current condition of the economy has placed additional pressure on Association budgets. Even so, studies show that it is much more cost-effective to address maintenance issues proactively rather than to seek to affect repairs after damage sets in when issues quickly turn from prevention to “emergency” repairs and responses. In fact, when maintenance is not properly conducted or is cut back due to poor planning or budgetary pressure, the failure of structures, parking surfaces, HVAC and other critical equipment will only increase over time.
The term preventive maintenance implies the systematic inspection and detection of potential failures before they occur. This term is the polar opposite of unplanned maintenance which is a response to an unanticipated problem or emergency.
A preventive strategy in addressing HOA and Condominium Association maintenance is meant to achieve at least three results: a safer environment due to common areas remaining free from defects, a lower cost of replacement, and a more efficient use of time, manpower and materials.
A Safer Environment
Certainly safety for all residents is a key criterion for association boards when considering what and when to implement maintenance activity. Rough or significantly uneven sidewalks, loose steps on stairways or wooden porches and decks, low-hanging tree limbs near parking spaces, broken tile around pools, and other such items simply must be granted priority attention on any repair list. Similarly, replacing broken or failed street and parking structure lighting, repairing video surveillance equipment, or addressing inoperable entry gates or security entrances, must also be the focus of first-priority repairs. Every such situation needing repair, especially those that could adversely affect the safety of the residents or guests of the community, must be given the prompt attention of those overseeing the common area elements of the association.
With such safety factors in mind, preventive maintenance is an essential tool that can actually look-ahead to those items which, if not kept in proper repair and appropriate working order, could result in excessive risk to people who live in or visit the association property. With these types of items, preventive maintenance is a tool that can keep adverse conditions from ever developing in the first place. As we commonly hear, this boils down to a matter of placing safety first.
A Lower Cost of Replacement
Having preventive maintenance programs can help to minimize or even eliminate sudden “emergency” repairs that result in after-hour or rush-order and extra costs to the association. Such a strategy can help to avoid major unplanned repairs and unknown malfunctions in the association’s common areas or common area equipment.
In contrast to urgent and unplanned repairs, preventive maintenance can help to maintain a constant work flow thus keeping labor and vendor costs in line with an annual budget plan since they can actually be scheduled on a seasonal basis, in accordance with a planned work schedule, and during normal work hours.
Preventive Maintenance Checklist:
- Gutter cleaning
- Power washing
- Touch up painting
- Siding repairs
- Water prevention (caulking)
- Deck and fence repairs
- Wood rot repair
- Dryer vent cleaning
- Drywall repairs
- Tile sealing and grout repair
- Changing light bulbs
- Irrigation repair
- Pest control
- House cleaning (common areas)
- Window cleaning
- Gutter cleaning
- Carpet cleaning (common areas)
- Duct and furnace cleaning and repair
This strategy should also include regularly scheduled inspections that follow routine seasonal schedules. These inspections can also be based on the annual budget, one that includes preventative maintenance; thus eliminating or at least drastically reducing surprise and reaction-based repairs that result in equally surprising costs or cost overruns.
Yet another way that preventive maintenance can save costs is that taking good care of existing common area elements can often extend the useful life of such elements. With simple routine maintenance it is often possible to expand the amount of time that key equipment and structures are able to be used in a productive manner. This can reduce the cost of replacement which more than justifies the minimal cost of the preventive upkeep that is routinely provided along the way.
Efficient Use of Time, Manpower, and Materials
Scheduled Inspections and scheduled preventive maintenance can be choreographed in a much more time and labor efficient manner. These efficiencies can save significant costs with both labor and materials. Obviously, when work is scheduled well in advance, the use of manpower can be coordinated and tasks can be group into common categories which can reduce wasted time and partial day trip or hourly charges.
In a similar manner, materials for maintenance and routine repairs can be ordered well in advance thus saving on rush-order charges or deliveries that are not properly matched to the availability of the workers assigned to the task.
Most, if not all, reserve studies will suggest or even specify items that need attention in the form of maintenance and repair. These elements can be translated into a seasonally appropriate time-efficient schedule that includes item-by-item checklists that make addressing each item a matter of a scheduled routine. In cases where the reserve study provider’s report does not include items that may need attention for maintenance, replacement, or repair in a given annual cycle, most quality service vendors will provide options that include inspections and proposed schedules to address elements that need attention. Simply make certain that such reports or service providers produce not only a list of needed repairs, but that they also supply the association with items where preventative maintenance would be recommended.
Summary
A preventive strategy in addressing HOA and condominium association maintenance can produce three productive results: a safer environment, lower repair and emergency replacement costs, and more efficient use of time, manpower, and materials.
As stated previously, the current condition of the economy has placed additional pressure on Association budgets. Keeping in mind that it is much more cost-effective to address maintenance issues proactively rather than to instituting repairs after damage sets in can help to save precious human and financial association resources.
When it comes to association maintenance and repairs, it truly is correct that an ounce of prevention is worth a pound of cure!
By Sean Hughes, Director of Operations, RW Handyman
About the Business
Have a question? Ask the experts!
Send your question