10 Terms You Should Know About Custom Injection Molding
By IMCO Inc
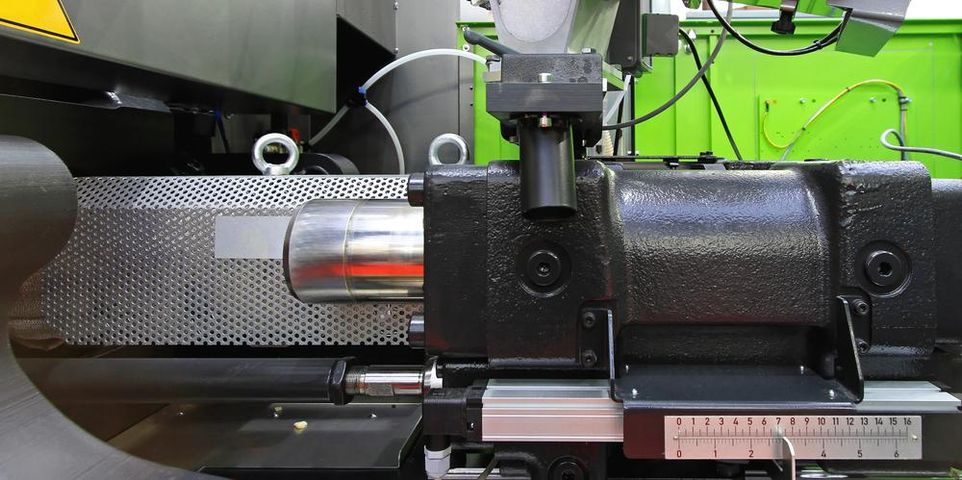
The process of custom injection molding is responsible for the production of many everyday objects in mass quantities, from toys to office supplies to furniture. It’s a quick and easy way to create products by injecting plastic material into a mold cavity, resulting in forms that perfectly match the original mold.
Despite the simplicity of the process, there’s a lot that goes into using injection molders. The plastic molders at IMCO Inc, based in Spencerport, NY, are here to share 10 terms associated with custom injection molding:
Gate: The gate is an entry point for the plastic material to enter the mold. After molding, the gate’s vestiges must be either manually or automatically detached.
- Boss: Some plastic molds feature small round projections that resemble tubes. These are known as bosses.
- Cavity: To create a piece of custom injection molding, the plastic material must first be injected into a concaved space called the cavity.
- Flash: The mold must close to create a sufficient product. Otherwise, a layer of plastic known as flash may develop on the outside of the mold cavity. Flash can occur if some product is released from the mold during the initial filling.
- Line of Draw: This refers to the specific direction that the mold cavity halves separate, allowing the plastic piece inside to release without interference.
- Runner: The runner acts as a tunnel that is designed for the plastic material to move from the injection molder, through the sprue, and finally to the gate.
- Sprue: The sprue is the section that connects the runner to the injection molder.
- Warping: Warping is an unfortunate side effect that occasionally occurs during custom injection molding. When this happens, the plastic piece may appear distorted or damaged, usually because of an issue during the cooling of the product.
- Shrink Rate: During this cooling process, the plastic injected into the molding shrinks. The shrink percentage is factored into the mold prior to the actual creation of the product.
- Core Out: Sometimes the end result isn’t what it’s supposed to be. Core out refers to the process of removing unneeded material from the resulting plastic part, either because it serves no purpose or it creates warp.
Do you have custom injection molding needs? Turn to the experts at IMCO Inc to find out how they can help you. Visit their website to learn more, or give them a call at (585) 352-7810.
About the Business
BUSINESS
Machine Shop
IMCO Inc
- - - - -N/A
(2 reviews)
15 Turner Dr., Spencerport, NY 14559
Have a question? Ask the experts!
Send your question