5 Materials Used in Plastic Injection Molding
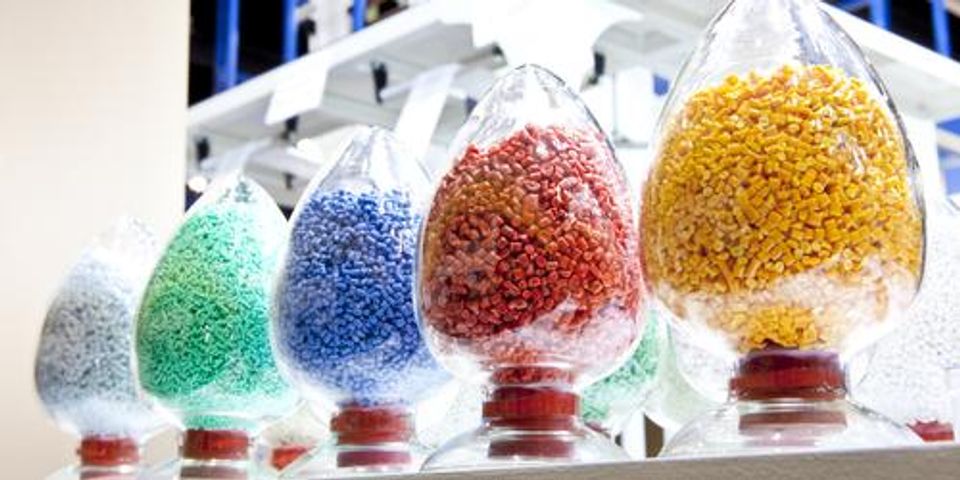
While precision machinery is largely responsible for the high efficiency of injection molding operations, the plastic resin materials are what determine the overall adaptability and performance of the final product. While available in a variety of colors, these materials all share a small granule shape that’s ideal for fast melting. But as Pacific Integrated Manufacturing explains, this similar appearance doesn’t mean all involved materials function the same way. To help explain the differences, this contract plastic injection molding service in San Diego, CA, highlights five of the most common industry materials and when they might be used.
5 Plastic Injection Molding Materials
1. Acetal
Acetal, or polyoxymethylene, is a tough thermoplastic used for engineering purposes because of its high tensile strength, such as in gears and fasteners. With high surface lubricity, acetal is ideal for parts that need to move reliably with minimal friction. Although this material is highly resistant to wear, it can warp under high heat and have problems bonding with other materials, such as glue.
2. ABS
Short for Acrylonitrile Butadiene Styrene, ABS is appreciated for heat-resistance and sturdiness. As a lightweight material, ABS is a good choice for injection-molded musical instruments, automotive accessories, canoes, and luggage. ABS is also ideal for use with metal—such as pipes—as the two components bond well together. However, ABS has poor resistance to chemicals, UV light, and electrical currents.
3. High-Impact Polystyrene
High-impact polystyrene is excellent for any producer that needs a highly customizable material at a low-cost. This material is typically found in display signs and kiosk structures, as the plastic lends itself to printing, gluing, and bonding.
4. Polypropylene
Unlike ABS, polypropylene is known to withstand exposure to electricity and chemicals, which makes it an ideal choice for household products and reusable containers. In addition, polypropylene has a greater resistance to fatigue than other materials, which is why it is commonly used in hinges and automotive applications. Despite these benefits, polypropylene is flammable and subject to UV damage.
5. Low-Density Polyethylene
Low-Density Polyethylene or LPDE is commonly found in household consumer goods, medical supplies, and electronic wiring. Highly flexible, chemical-resistant, moisture-resistant, and tough, this plastic is incredibly versatile and be used in a diverse range of applications. On the other hand, LPDE does not adhere well to other materials and can face damage when exposed to high heat or severe weather.
Once you’ve determined which plastic resin is best for you, you need to find a reliable manufacturer to provide precision injection molding. Serving medical and science companies, Pacific Integrated Manufacturing is a trusted resource for organizations seeking end-to-end plastic injection molding services in the San Diego, CA, area. Operating out of a well-equipped 50,000-square-foot plant, this team can quickly adjust production to meet the demands of your project—including your resin material choice. Learn more about their capabilities online or call (760) 822-3341 to discuss your project.
About the Business
Have a question? Ask the experts!
Send your question