How Have Plastics Impacted Health Care?
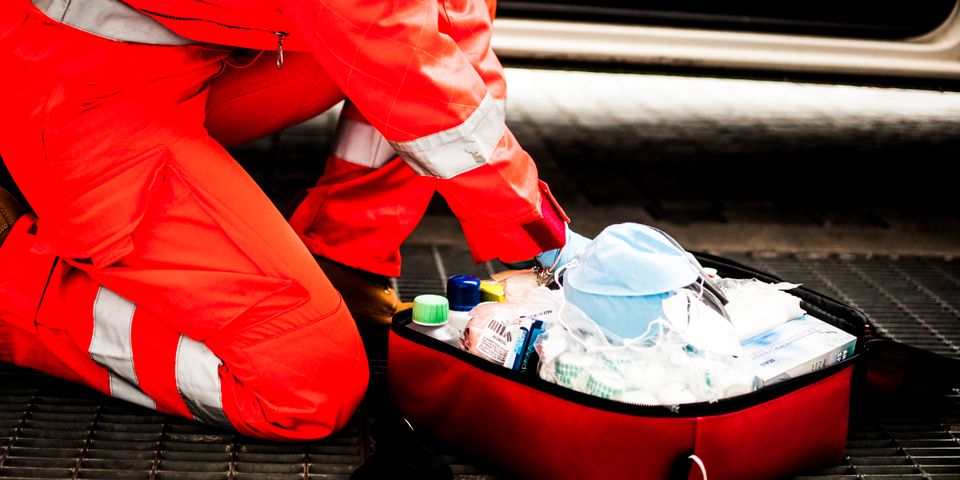
From children’s toys to electronics, plastics are one of the most widely used materials today. However, the medical field is where they make the biggest impact. Plastic medical devices only came into use in relatively recent history, but they have changed the industry forever. Here’s a closer look at why medical manufacturing companies rely on plastic today.
A Guide to Plastic in the Medical Industry
What Was Common Practice Before Plastic?
Before plastic came onto the scene, metal was the most-used material for medical devices. From surgical tools like scalpels to the silver catheters used in early Greek civilization, this material was reliable but heavy and rigid. In the 1930s, ceramics became more popular thanks to their durability and ability to stay cool, and they soon began to replace metal for use in bone and dental implants. Transparent glass was also key for vials, tubes, and other storage devices. Plastic didn’t become a common medical material until the mid-20th century.
What Are the Current Benefits?
Plastics were an instant hit in the medical field thanks to their malleability. Unlike glass, ceramics, and metal, plastic is much better at accommodating the curves, angles, and irregular shapes of the human body. It’s also lighter and less vulnerable to breakage if dropped in a bustling hospital environment. From IV tubing and bags to catheters, polyvinyl chloride (PVC) plastic is widely used in a variety of medical facilities. Not only is plastic more flexible, but it’s also not vulnerable to chemical reactions like corrosion, and it won’t erode in the presence of acids, bases, lipids, or alcohols. Also, single-use plastic equipment like syringes can be discarded immediately. Metal and glass syringes had to be reused for the sake of cost-efficiency, but this came with an increased risk of spreading infections.
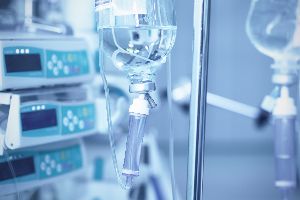
What Are the Newest Implementations?
These days, manufacturing companies are continuing to tap into plastic’s potential as a medical material. For example, the advent of 3D printing technology allows for the rapid production of custom plastic pieces. From dental molds to stents and joint replacement devices, plastic can easily be set into a specific shape just by creating a drawing and submitting it to a machine. While 3D printing essentially draws objects out of thin air, injection molding creates plastic items by injecting liquid plastic into a mold and allowing it to harden. Metals, ceramics, and glass don’t have the flexibility needed to complete these projects with ease, and they would require much more extreme temperatures or pressures to re-form.
If you’re looking for a reliable manufacturing company that fashions medical devices out of plastic, reach out to Pacific Integrated Manufacturing in Bonita, CA. They have over 15 years of experience with medical devices, from plastic injection molding to assembly services, and their 50,000-square-foot plant operates under rigorous inspections and tests on all items. Visit the website to learn more about their cost-effective offerings, or call (619) 921-3464 to ask for a free quote.
About the Business
Have a question? Ask the experts!
Send your question