3 Medical Injection Molding Techniques
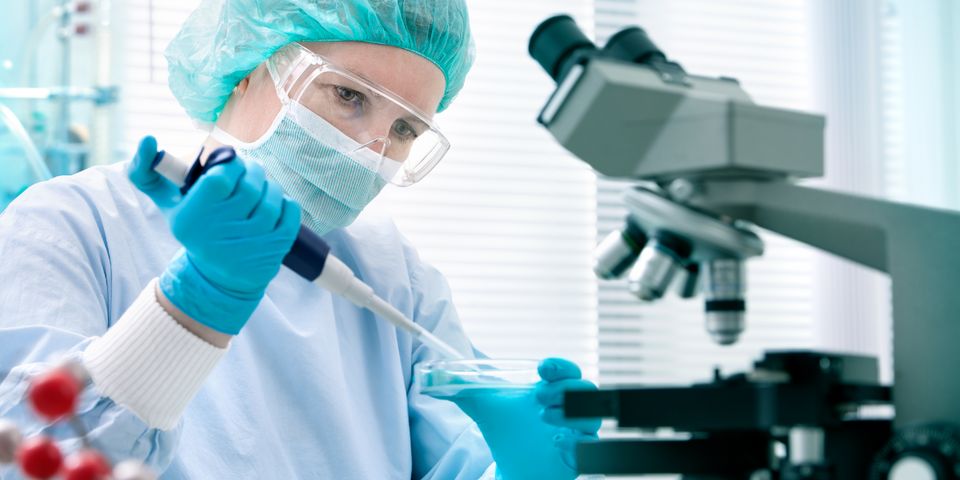
Plastic injection molding is a technique used in the manufacturing of medical and pharmaceutical products. This efficient process involves squeezing heated thermoplastics into metal molding, cooling the mold, and ejecting the part. It’s used to create laboratory supplies, surgical equipment, medical enclosures, and other vital components, and it can accommodate a variety of different plastics. Here are three common techniques.
Medical Plastic Injection Molding Techniques
1. Thin Wall Molding
This technology is used to create plastic components with thin walls, such as tubes and vessels. The process produces resilient products that are lightweight and compact but don’t sacrifice strength and durability. The technology can also create larger components, including panels. Thin wall parts create more room inside medical devices for mechanical and electrical components. Molding professionals use a high-flow thermoplastic with a low melting point and a robust constitution that prevents failure due to heat exposure.
2. Gas Assist Injection Molding
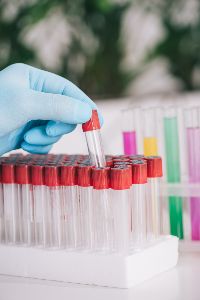
This process involves injecting either carbon dioxide or nitrogen into a mold. This produces thick, resilient walls suitable for the creation of larger, more complex plastic parts of medical devices. It’s especially useful for objects with complex shapes or detailed textural finishes. It’s simpler to produce large parts through gas assist injection molding because supportive elements, such as ribbing or other textured refinements, can be molded into the finished product. The result is a more stable and dependable product.
3. Overmolding
Some products require more than plastic in their construction, including syringes, tubing, and dental devices. Overmolding supports this design by combining plastic with another material, such as metal or rubber. The process involves layering the base material first, then adding the other material over it. In the medical industry, it’s often used to create a tough, scratch-resistant or waterproof housing over a softer material.
Overmolding's benefits include the ability to absorb shock, noise, and vibrations with greater efficiency. It also minimizes production time because the second material is molded with the first in one session. There’s no need to manufacture each part and then assemble them.
If you seek reliable professionals for plastic injection molding, turn to Pacific Integrated Manufacturing in Bonita, CA. In their 50,000-square-foot facility, they provide reliable injection molding, assembly, and packaging services for the health care and life science industries. Visit the website for more on their medical device manufacturing process, or call (619) 921-3464 to request a quote.
About the Business
Have a question? Ask the experts!
Send your question