4 FAQ About Ultrasonic Welding
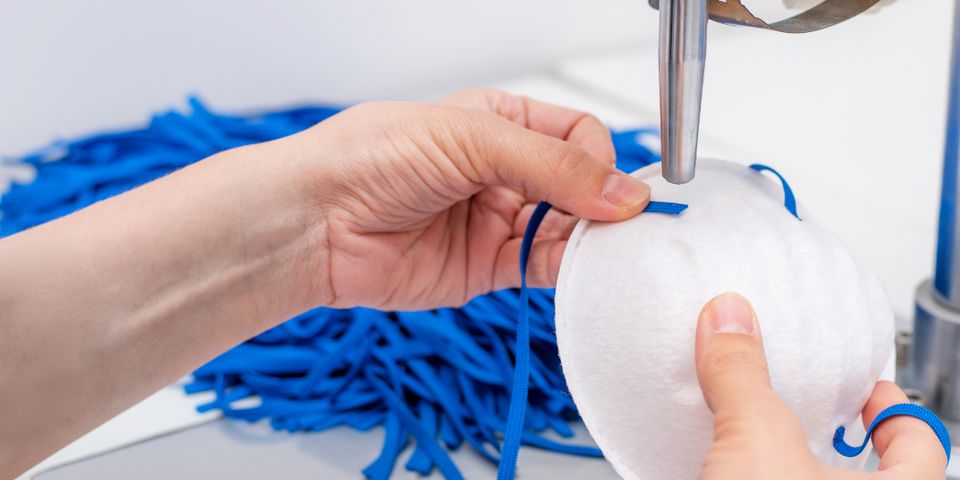
Ultrasonic welding is the process of using heat produced by high-frequency mechanical movements to join thermoplastics. It is used in a variety of industries and products where superior sealing performance is essential, such as medical device manufacturing. If this is a new component of your business, you may have questions about the process and its benefits.
What You Need to Know About Ultrasonic Welding
What does the process involve?
First, the two thermoplastic components to be welded are placed atop one other in an arrangement called a fixture. Next, a titanium or aluminum device called a horn is brought into contact with the uppermost part of the fixture. Then, the technician applies controlled pressure by clamping the horn against the fixture. The horn is vibrated vertically for a predetermined amount of time, with the vibrations moving through the thermoplastic to the joint interface to generate friction and heat. Once the material reaches its melting point, the vibration stops, and the melted plastic cools and hardens to complete the weld.
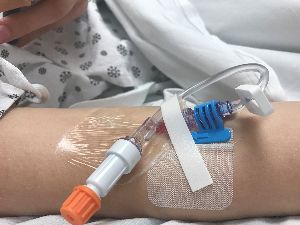
How is ultrasonic welding used in medical device manufacturing?
A number of common medical products are manufactured with this technology. These products include arterial, anesthesia, and blood filters; catheters; dialysis tubes; face shields; and even textiles, like hospital gowns, masks, and transdermal patches.
What are its benefits?
Ultrasonic welding is fast and efficient, and it provides exceptional sealing performance. Because it does not use glues, solvents, or other toxic chemicals, it is environmentally safer and cleaner as well. It is also one of the most affordable plastic welding options on the market due to its relatively simple implementation, low fault rate, and low production costs.
Is ultrasonic welding stronger than glue and solvents?
In most cases, the plastic joint you get from ultrasonic welding is stronger and more dependable than any connection that a glue or solvent could provide. The technique allows for a tight, uniform seal within seconds. As long as the thermoplastic has a thin to moderate thickness, this technique can give your devices the reliable, sturdy seal they need to function effectively.
Experience the benefits of ultrasonic welding for your business's products. Pacific Integrated Manufacturing Inc. in Bonita, CA, has been providing this service for over 20 years, along with their plastic injection molding, assembly kitting, and custom automation cell services. Find out why they are a global leader in medical device manufacturing by calling (619) 921-3464 or visiting them online.
About the Business
Have a question? Ask the experts!
Send your question