A Guide to Dry Rooms In Medical Device Manufacturing
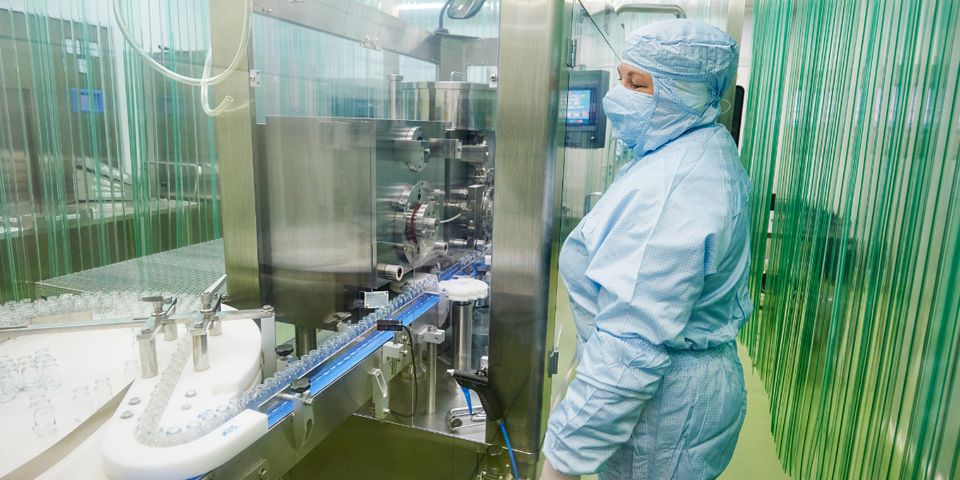
When it comes to manufacturing medical devices, the proper temperature settings in the facility are a must for safe and efficient production. This is where a dry room provides the humidity controls needed to see construction through to success. The following guide highlights how these specialized interior environments work and the important role they play in medical device manufacturing.
What Is a Dry Room?
The room is a hermetically-sealed space that is designed to maintain low levels of humidity. They are also constructed with particle filtration systems to ensure the interior is 100% free of air pollutants and other impurities. Dry rooms are primarily used for specialized production purposes such as for medical device manufacturing.
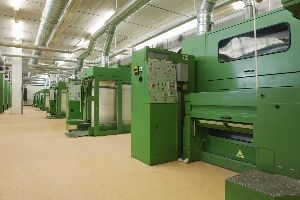
Some features installed will typically include a range of air ducts for certain filtration measures. For example, return air and supply ducts are tightly sealed and insulated to help prevent thermal loss and moisture formation. Exhaust air ducts absorb hot and moisture-laden air from dehumidification while make-up ducts disseminate fresh, impurity-free air throughout the dry room to further eliminate the exhaust coming from manufacturing equipment.
Dry rooms are also equipped with condensing or heat-rejection systems to remove heat loss from equipment, dehumidifiers, lighting fixtures and even body heat. As a further safeguard for keeping moisture from entering the space, the walls are customized with fire-retardant materials, airtight seals, and metal-reinforced insulation.
What Is Its Role In Medical Device Manufacturing?
There are industry regulations in place to ensure the safe construction of medical devices that are used by patients, physicians, and other healthcare practitioners. The U.S. Food and Drug Administration(FDA) and the International Council for Harmonization of Technical Requirements for Pharmaceuticals for Human Use (ICH) also have a list of comprehensive standards for assuring products meet physical and chemical testing thresholds.
Dry room that are used for medical device manufacturing must have a number of safeguards in place. These include humidity and temperature chambers and quality control systems. There are also several types of analysis the devices must undergo after development in a dry room, such as for failure, migration, stability, storage, packaging, and purity.
All the strict governmental and industry guidelines for developing devices for use in the medical field are vital to protect their long-term integrity and are deemed safe for individuals to operate.
Pacific Integrated Manufacturing in Bonita, CA, specializes in medical device manufacturing, including through the use of dry rooms. For more than 20 years, the company has served the healthcare sector with its state-of-the-art production systems such as injection molding machines. More than 300 trained employees are certified in the development and assembly of medical devices while following safety and testing regulations. To learn more about their services and how they can meet your manufacturing needs, visit the website for a virtual tour or call (619) 921-3464 to speak to a knowledgeable representative.
About the Business
Have a question? Ask the experts!
Send your question