3 Ways to Improve Hospital Supply Room Inventory Management
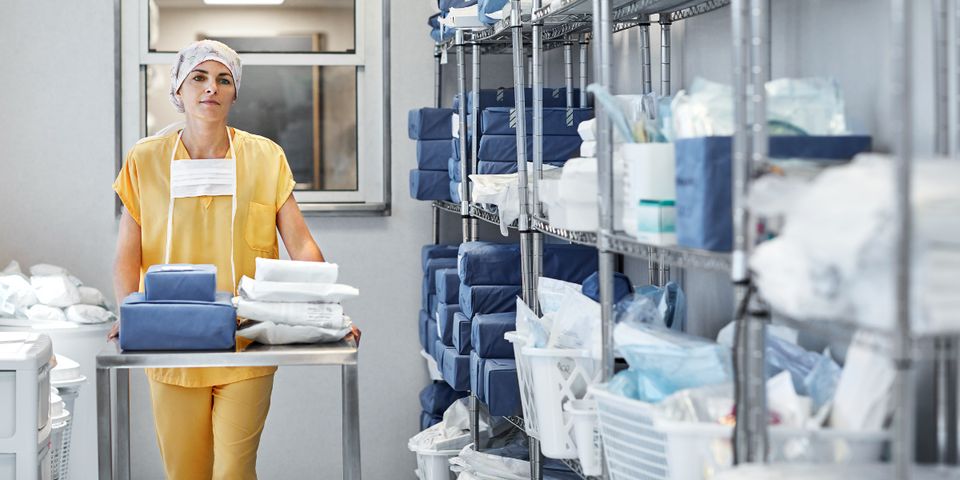
Manufacturing companies make plenty of items used daily in hospitals across the country. Unfortunately, most hospitals are overwhelmed by the number of things that must be used, tracked, replenished, and trashed. Due to poor hospital supply room inventory management, medical centers tend to overspend on items they already have or do not need. However, it's possible to improve inventory management with these tips.
How to Boost Hospital Supply Room Inventory Management Efficiency
1. Track Specific Inventory Metrics
Most hospitals can save a substantial portion of their budget by cutting down on their supply room inventories without emptying them entirely. To have a lean supply room, hospitals should measure inventory key performance indicators (KPIs) to determine which materials they use most often.
Total inventory per year and monthly inventory turnover are the essential KPIs to track. They will show the hospital staff how often the inventory turns over each year and each month. Midsize hospitals turn over supply room inventory between two to eight times a year. However, four to eight times annually is ideal for keeping the supply room stocked without too many excess products.
2. Simplify Inventory Management Tasks
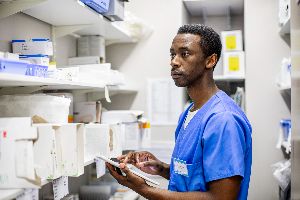
Health care providers and staff spend a significant amount of time handling inventory-related tasks during their shifts. The more time they spend managing the supply room inventory, tracking tools, or ordering materials unnecessarily, the less time they have to devote to patients.
Streamlining inventory management can free up precious time for clinicians. The best way to simplify and streamline inventory management is to ensure everyone on staff understands their role and responsibility as it relates to the supply room. Once everyone knows the hospital's expectations, the supply room must be recognized to ensure frequently used materials are on the front shelves at eye level. If the hospital wants to apply asset tags or barcodes to the inventory items, during the reorganization project is the ideal time to do it.
3. Laser Mark Stainless Steel Tools and Other Items
Barcodes engraved, etched, or inked into hospital tools and equipment help determine their appropriate storeroom location. The barcodes also allow hospital staff to track the whereabouts of stainless steel tools and other materials if someone takes them out of the supply room.
Laser-etched barcodes are best for metal tools because they are more durable and hygienic than sticker labels. Consider adding relevant information to the barcode, such as storage requirements, storage location, stock level, and expiration date, if applicable.
As one of the leading manufacturing companies in Bonita, CA, for over 15 years, Pacific Integrated Manufacturing is the go-to source for medical device manufacturing, pipette tips, and other thermoplastic supplies in bulk. The manufacturing company has a 50,000-square-foot plant specializing in precision injection molding and assembly services for the science and medical sectors. The facility boasts a quality-first policy with a thorough screening process to ensure customer satisfaction. Call (619) 921-3464 for a free estimate, or visit them online to learn more about their services.
About the Business
Have a question? Ask the experts!
Send your question