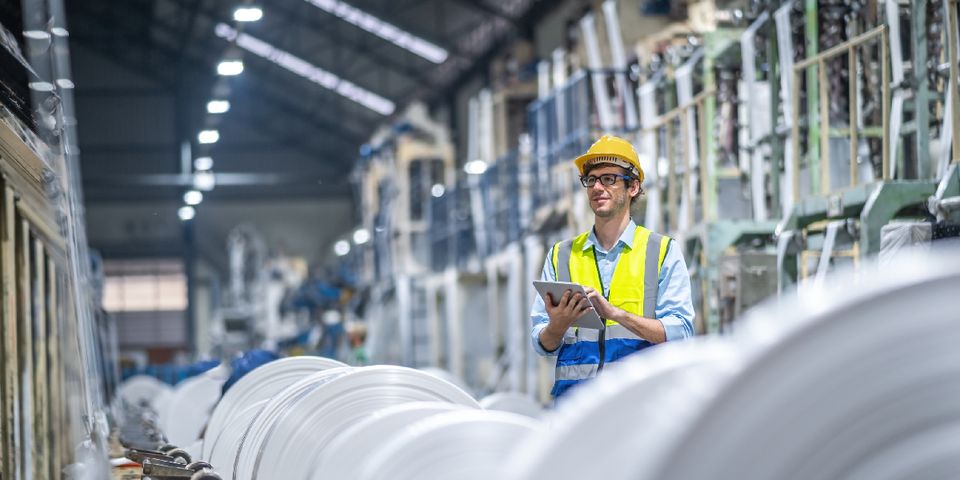
Thermoforming is a versatile and reliable practice used in various industries, from automotive to health care. With this technique, a manufacturing company can produce custom materials of different sizes, colors, and characteristics using thermoplastics. Here is a guide to this process and the various items it can create.
The Process
Thermoforming involves heating and stretching thermoplastic over a mold to create a desired shape. It is restricted to producing thin-walled designs, even thickness, and versatility for manufacturing parts with complex geometry. Various processes are used to form plastics, with the most popular types including vacuum, pressure, mechanical, drape, matched mold, twin sheet, and billow.
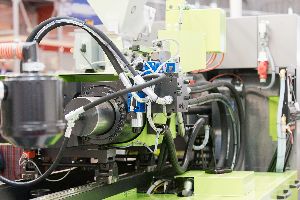
The technique a manufacturing company utilizes depends on the requirements of the project. For example, they could turn to mechanical or billow forming for products requiring high-quality precision. The former uses a core plug to shape the plastic, forcing it into or around the mold, while the latter is a free-form technique that uses air jets.
As for simple-shaped goods that don't require extreme accuracy, a manufacturer will create them using a vacuum- or drape-forming technique. Both are quick, cost-effective solutions for low- to large-volume productions. While the vacuum process involves pulling out air to shape the plastic sheet against the mold, the drape method requires the material to get pressed, bent, or formed over a mandrel.
Common Applications
Thermoforming allows manufacturers to produce small to large volumes of goods at affordable costs. The industries that benefit from this process are numerous due to the various items it can create. Here are some of the most common equipment that thermoforming produces:
- Agricultural: Interior components for tractors, feeding containers, and livestock housing.
- Automotive: Dashboards, bumpers, truck beds, and floor mats.
- Medical: Covers for equipment like IV pumps and ventilators, sterile packaging, and hospital room panels.
- Recreational: Playground components, canoes, and RV external parts.
If you're in the life science or health care industry and need reliable plastic injection molding services, turn to Pacific Integrated Manufacturing in Bonita, CA. For over 15 years, this manufacturing company has provided cost-effective and convenient solutions, including assembly kitting, packaging, material procurement, thermoplastics, and sterilization management. Visit the website to learn more about their services, and call (619) 921-3464 for a free quote.
About the Business
Have a question? Ask the experts!
Send your question