Exploring the Essentials of Plastic Injection Molding in the Medical Industry
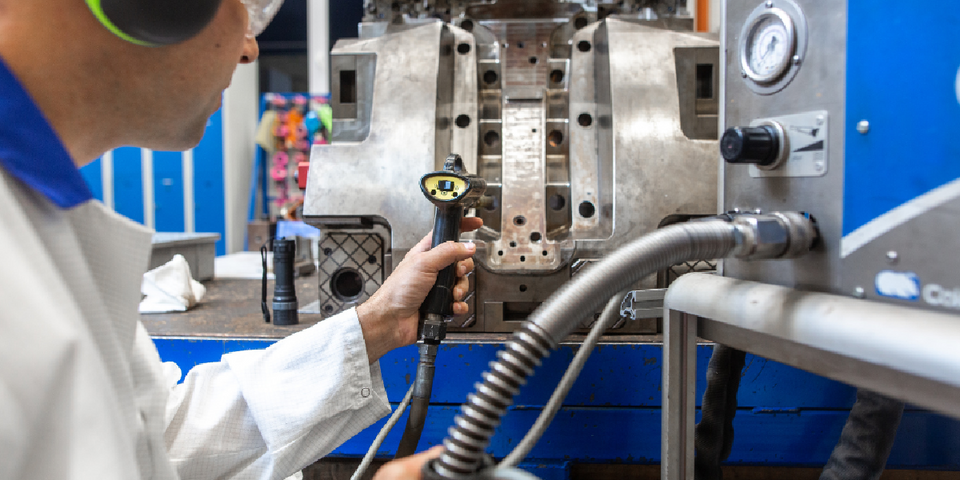
When it comes to manufacturing medical devices, plastic injection molding is a critical process. It plays a pivotal role in producing a wide range of medical components and equipment. If you're curious about this crucial aspect of the medical industry, here are 10 things you should know about plastic medical injection molding.
Plastic Injection Molding
1. Precision is Paramount
Plastic injection molding involves the precise injection of melted plastic into a mold to create intricate medical components. This process requires high precision and accuracy to ensure the final product meets strict medical industry standards.
2. Versatility is Key
One of the major advantages of plastic injection molding is its versatility. It can produce an array of medical parts, from syringe barrels to intricate implant components. The ability to create complex geometries makes it a valuable manufacturing method.
3. Material Matters
Plastic injection molding utilizes various materials, each with specific characteristics. Medical devices often require biocompatible, sterilizable materials. Understanding the material properties and selecting the right one is crucial to ensure product safety and efficacy.
4. Regulatory Compliance
Medical devices are subject to rigorous regulations and standards. Plastic injection molding must adhere to these regulations to ensure the safety and effectiveness of medical components. Quality control and traceability are critical.
5. Cost-Effective Production
Plastic injection molding can be a cost-effective method for mass production. The ability to create large quantities of medical components in a single run can lead to significant cost savings for medical device manufacturers.
6. Rapid Prototyping
In the medical field, quick product development is often crucial. Plastic injection molding allows for rapid prototyping, enabling manufacturers to test and iterate designs before mass production.
7. Sustainability Considerations
As the world becomes more eco-conscious, sustainability is a key factor in plastic injection molding. Many companies are adopting environmentally friendly practices and materials to minimize the environmental impact of their production processes.
8. Design for Manufacturability
To optimize the plastic injection molding process, it's important to design medical components with manufacturability in mind. Considerations like draft angles, wall thickness, and undercuts can affect the quality and cost of production.
9. Assembly Integration
In some cases, medical devices require assembly after injection molding. Integration of assembly processes is an important consideration in the overall manufacturing strategy.
10. Partner with Experts
For successful plastic injection molding in the medical industry, partnering with experienced manufacturers is crucial.
Plastic injection molding is a pivotal process in the production of medical devices. It offers precision, versatility, and cost-effectiveness while adhering to strict regulatory standards. Pacific Integrated Manufacturing Inc., located in Bonita, CA, specializes in plastic injection molding and assembly services, ensuring that medical device manufacturers receive high-quality components that meet industry standards. Contact them on their website or call (619) 921-3464 today.
About the Business
Have a question? Ask the experts!
Send your question