3 Tips for Addressing Common Polymer Problems
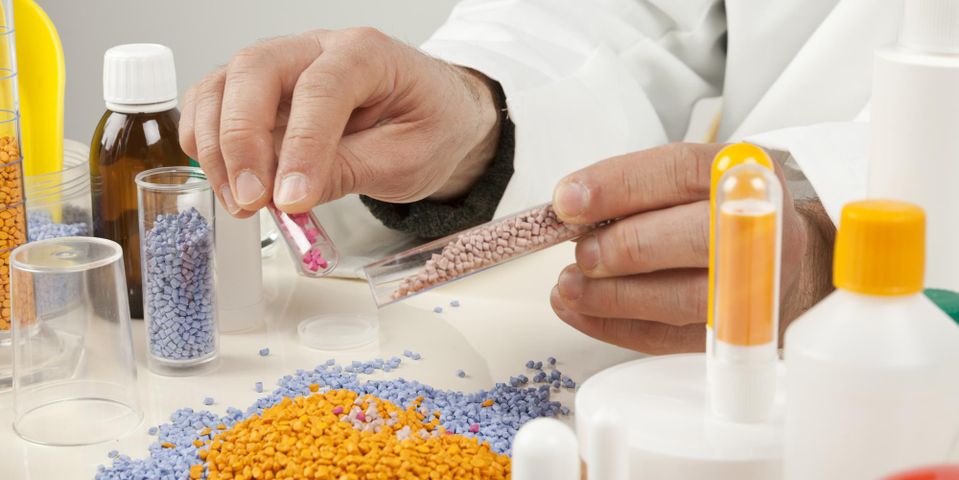
Polymers are used in the manufacturing of products ranging from nylon stockings to pacemaker implants. When it comes to medical device manufacturing, developers can face a variety of challenges using polymers such as epoxy and polyethylene. Certain design specifications for these plastic substances can cause loss of durability, changing shape, or compatibility issues during production and assembly. By keeping the following information in mind, those in this field can prepare for and adjust their procedures to accommodate these common polymer problems.
3 Polymer Design Problems to Keep in Mind
1. Expect Deviations
Medical device manufacturing using polymers is an unpredictable process because of the material’s vulnerability to such factors as moisture, heat, and pressure. For example, previous attempts at creating pacemaker implants using a polymer-based epoxy resin caused the material to swell and dissolve inside the human body. The production team then changed to a ceramic and titanium polymer instead, which provided more durability without affecting the human body. Expect landing on the right materials to take some trial and error.
2. Be Careful With Color Changes
Adding a color additive to a polymer can jeopardize the final results of a product. While changing the color during the manufacturing process is possible, producers should understand that they risk creating an unstable chemical makeup that can cause the product to crack, break, or shatter.
3. Accommodate Thermal Expansion
Many polymers used in medical device manufacturing can expand up to 10 times their original size when subjected to high temperatures or moisture. Designers should consider this and anticipate differential expansion. Determining the temperature at which parts will be validated before the process begins.
The medical device manufacturing experts at Pacific Integrated Manufacturing in Bonita, CA, specialize in reliable, quality production services for biomedical and life science companies. For more than 15 years, they’ve provided plastic injection molding and assembly packaging for clients across the world. They’ll help you find the right polymer materials for your project and see it through to completion with their efficient Kanban techniques. Call (619) 348-5373 or contact them through their website to learn more about their cost-effective practices.
About the Business
Have a question? Ask the experts!
Send your question