A Guide to Plastic Injection Molding
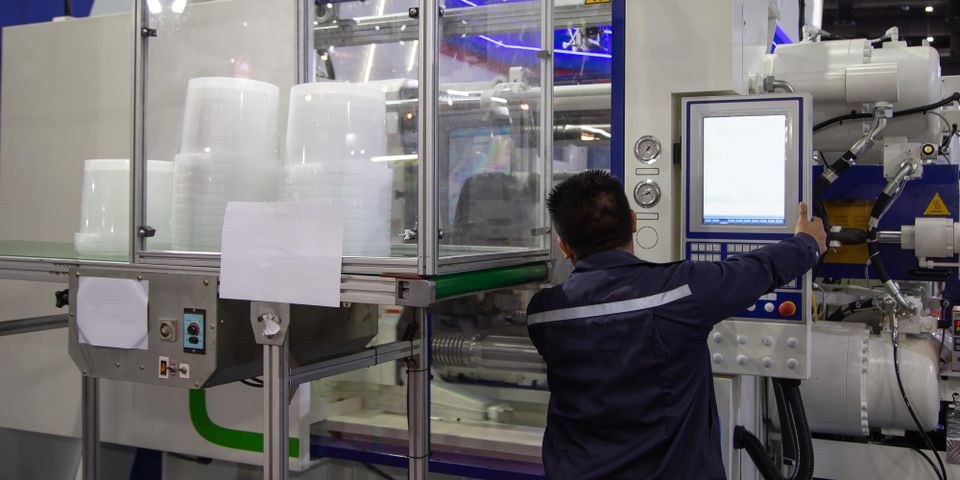
For businesses, fabricating parts and products is a costly endeavor, which is why they partner with manufacturing companies with access to advanced tools. One method of creating goods is plastic injection molding. Here’s a close look at how the process works and its benefits.
What Is It?
Plastic injection molding is a type of mass-production process designed to create the same item or part. As the name suggests, it injects molten polymers or resins into the mold specially made for the product. Using a custom-made pattern, you can produce large volumes of identical objects or even related components.
Production begins with the development of the mold itself. You have to consider the design and features before creating the pattern, so it will take time to perfect it. With the prototype, you can do an initial production run to see how the final product will look and determine whether the molding requires refinements or revisions. The steel-made molding tool is difficult and costly to change once created.
Once you have the mold, manufacturing can now start. To better picture the process, the injection machine has three parts—the feed hopper, screw, and heated barrel. Plastic injection molding uses thermoplastic and thermosetting polymers, fed into the heated barrel by a hopper. Because of the high temperature, the resins melt, compress, and get pushed forward by the screw into the mold cavity. After cooling, the part solidifies and is ejected.
Why This Process Is Beneficial
Plastic injection molding offers many advantages over other manufacturing processes, such as the ones below.
-
Cost-Effective: Excluding upfront costs with mold development, it’s a process that allows you to produce at high volumes without the exorbitant expenses. Since it’s automated, you save on overhead costs, too.
-
High Output: A primary reason for choosing this method is its capability to manufacture high volumes. An injection machine can do production runs continuously, and a single mold can produce different components as well.
-
Fast Production Time: Even products with complex or detailed features can be produced quickly.
-
Consistency: Because the injection machine creates objects from a single mold, expect a consistent quality across thousands of outputted units.
-
Low Scrap Rate: Compared to other production processes, plastic injection molding yields minimal scrap materials. Those it does make can be reused in the next run.
When you need customized medical products, get in touch with Pacific Integrated Manufacturing. A manufacturing company in Bonita, CA, they perform an extensive range of contract manufacturing services, including plastic injection molding, assembly packaging, and material procurement, to clients in science, medical, and diagnostic industries. Call (619) 921-3464 to get a free quote or visit them online for more on their capabilities.
About the Business
Have a question? Ask the experts!
Send your question