4 Qualities of Medical Device Manufacturing Design
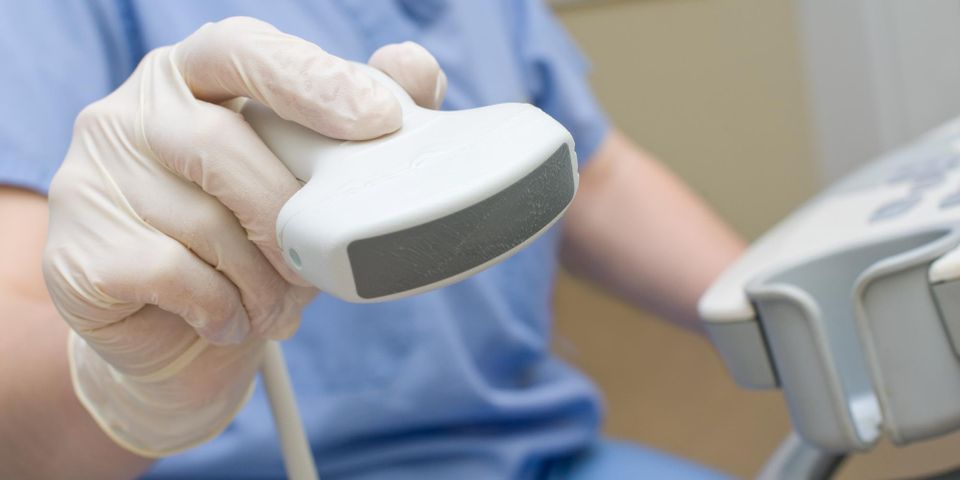
While all products should be crafted in a way that’s safe and practical, these qualities are particularly important when designing medical devices that prevent or manage health risks. That’s why, if you’re developing one of these resources, work with specialists to ensure your product is one that can be used dependably by health care professionals and patients. Before you take your plans to a medical device manufacturing provider, here are four design tips you’ll want to review.
What Design Factors Should You Consider Before Medical Device Manufacturing?
1. User Safety
Whether a device is being used by a patient, caregiver, or medical provider, it must always be safe to use. For example, you may need to make sure moving parts won’t break apart in the patient’s body or pinch fingers during use. Materials also shouldn’t be prone to overheating. And if the equipment uses electrical resources, all wires and connectors must be properly insulated to prevent accidental shocks.
Since there is a wide range of safety factors, consult a safety engineer during the design period. With a thorough understanding of ISO 14971 standards, these professionals run exhausting testing to identify risks.
2. Accuracy
If medical equipment needs to move in a specific way, measures body functions, or delivers medication, its overall accuracy could mean the difference between life and death for a patient. For example, insulin pumps must be able to produce a specific amount of this hormone, while cardiac monitors should report precise real-time data of heart functionality.
Part of making sure your tools deliver the same results time and time again is to partner with a medical device manufacturing company that utilizes top-tier accuracy-control solutions—such as precision injection molding and pad printing.
3. Wear
Once prototypes are ready, testing must be performed to see how materials wear with long-term use. For example, weak plastics may eventually break over time. Devices with caster wheels, on the other hand, should be able to travel long distances without sticking or producing noise.
4. Ease-of-Use
While some medical devices may be complicated, those that are used by patients should be intuitive and adaptable. Nebulizer parts, for instance, should feature plastic moldings that indicate the proper areas to connect parts—such as the tubing, nebulizer cup, and mouthpiece.
Devices that use switches, knobs, or handles should also be easy for various individuals to operate. For example, when a person with arthritis uses a device, they should be able to maintain a firm, comfortable grip without experiencing pain.
Based in Bonita, CA, Pacific Integrated Manufacturing offers an expansive production facility for medical devices. Whether your project requires precision injection molding or high-volume assembly kitting, these experts will deliver results that are reliable, cost-effective, and compliant with industry standards—such as those laid out by the FDA. To learn more about their manufacturing capabilities, visit this plant online or call an associate at (619) 921-3464.
About the Business
Have a question? Ask the experts!
Send your question