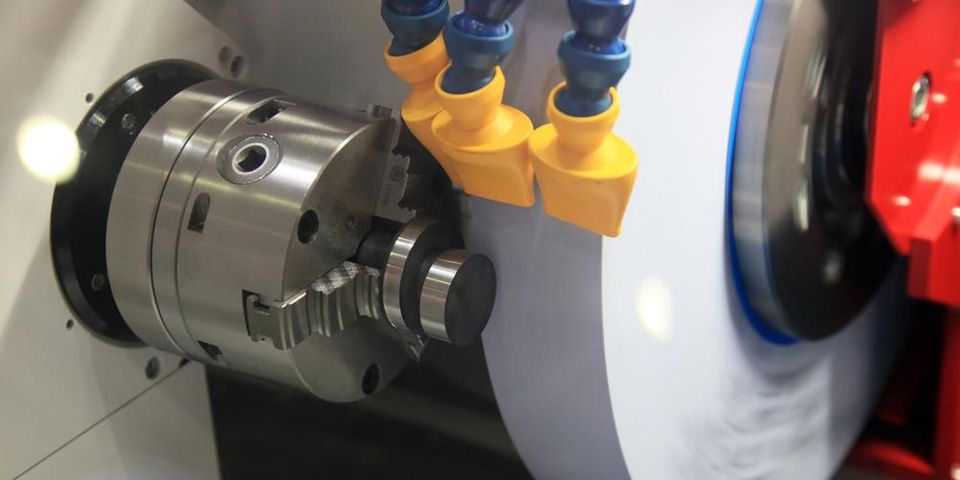
If you’re involved in the medical, aerospace, or hydraulics industries, you’ve probably encountered the grinding process at some point in your work. While cylindrical is standard, centerless grinding has its own specialized applications. LWG Finishing in Fairfield, OH, knows that most of their clients are unfamiliar with the ins and outs of this specific process. Here, they delve into the basics of centerless grinding.
What Is Centerless Grinding?
This process is typically used in situations where precise roundness is essential, such as in the production of auto parts. Parts like pistons and valve spools must be accurately shaped to function properly, and cylindrical grinding guarantees this. Before the process came into practice, rounded pieces had to be held or gripped by other fixtures when worked on. With centerless grinding, these parts are simply inserted between two wheels and rested on a sloped support.
How Does It Work?
Through a process called in-feed grinding, one wheel pulls the piece being manipulated against a dead stop as the other wheel grinds the part into the desired size. The absence of a gripping fixture allows laborers to load pieces much faster, as well as produce longer and thinner results. Plus, since the workpiece gravitates to a natural center between both wheels, the finishing process is simplified. For the best results, this manufacturing process should be handled by an experienced professional with time-tested skills.
If you’re interested in implementing centerless grinding into your own business, contact LWG Finishing today. This trusted company specializes in chrome plating and offers a wide range of services to everyone, from mining to automotive clients. With almost 50 years of experience serving the Tri-State area, they can ensure you’ll be satisfied with the finished product. For more information on their work, call them at (513) 860-1156 or visit their website.
About the Business
Have a question? Ask the experts!
Send your question