A Brief Comparison of Electrolytic & Electroless Nickel Plating
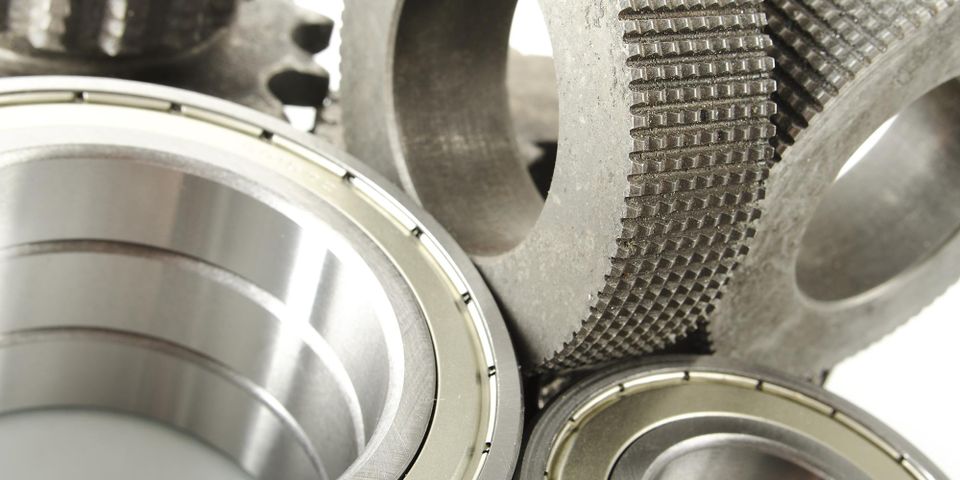
Nickel plating boosts the performance of metal parts and objects, making them less susceptible to corrosion, overheating, and wear. Coatings can be applied in one of two ways. If you’re wondering about the differences between electrolytic and electroless nickel plating, here’s an overview to help you choose the best solution for your project.
Electrolytic vs. Electroless Nickel Plating
Process
With electrolytic nickel plating, a part is placed in an electrolyte bath along with a bar of nickel. A wire with a negative electrical charge is attached to the part, and a positive charge is connected to the nickel. Once active, the electrical current pulls nickel ions from the solution and deposits them to coat the surface of the part.
Electroless plating doesn’t use electricity. Instead, technicians place a part into a bath containing a nickel-phosphorous alloy and other chemicals. Once submerged, a chemical reaction causes the nickel to adhere.
Materials
Parts placed in electrolytic baths must be conductive. As such, metal is the only viable substrate for electrolytic nickel plating.
Electroless methods permit technicians to adjust chemical baths to produce different nickel deposition outcomes. Both metal and plastic parts can be plated using this approach.
Uniformity
During electrolytic plating, ions are attracted to surfaces with the highest current. Raised edges and corners of parts may collect more of the metal than other areas, resulting in uneven coatings. Lack of coating uniformity may impair the functionality of the part, creating unnecessary friction during mechanical operation.
With electroless plating, the coating is always uniform. No matter the shape of the part, technicians can achieve a smooth, even finish, delivering maximum durability and corrosion resistance.
Corrosion Resistance
Although both methods of plating improve a part’s corrosion resistance, electroless baths produce better results. The lack of uniformity associated with electrolytic processes may make the nickel somewhat thinner and more porous in some spots, increasing the risk of moisture penetration.
Hardness
Electroless nickel plating generally produces harder coatings than electrolytic plating, too, which also increases a part’s durability and performance.
Specializing in industrial metal finishing, Porter-Guertin Co. is a leading resource for electroless nickel plating in the Cincinnati, OH, region. Their highly trained technicians use state-of-the-art equipment to refine plating processes, delivering superior consistency and corrosion resistance. They’re also capable of tailoring their methods to produce custom results, such as increasing plating thickness or coating specified areas. To learn more about their nickel and hard chrome plating solutions, visit this metal finisher online, or call (513) 241-7663 to speak to the team.
About the Business
Have a question? Ask the experts!
Send your question