How to Maintain Electric Motor Bearings
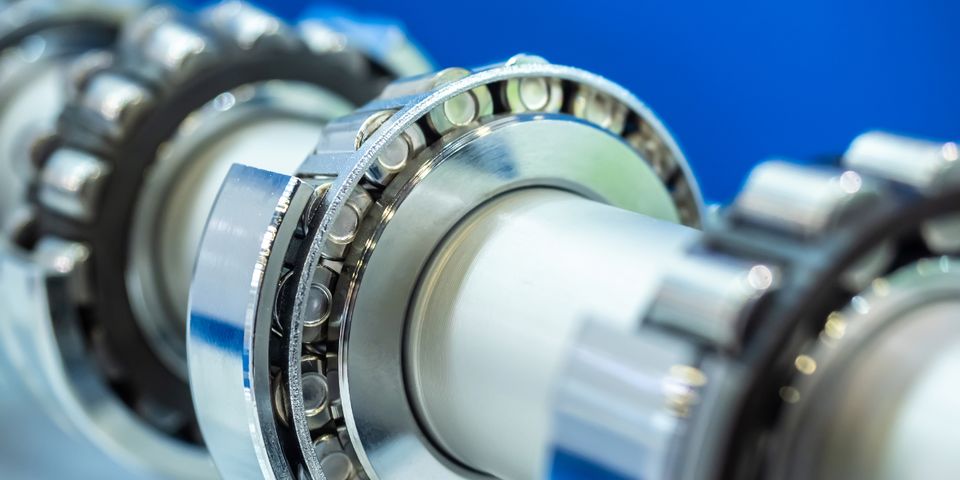
As small components responsible for reducing friction and transferring motion between moving components, bearings play an incredibly important role in electric motor function. But while these parts are designed to withstand heavy use for several years, more than half of electric motor failures are related to issues with the bearings. Fortunately, most of these instances can be avoided by providing the bearings with basic routine care. Here are some ways to address this important aspect of electric motor maintenance.
3 Tips for Electric Motor Bearing Maintenance
1. Minimize Operational Stress
High-quality bearings can resist wear for many years if they don’t face constant friction during activity. To minimize operational stress, follow your system’s electric motor maintenance and cleaning schedule to keep abrasive contaminants—such as dirt and chemicals—from reaching the bearings.
It’s also critical to follow proper lubrication steps according to your motor’s product manual. Under-lubricating will cause bearings to experience too much friction, which can generate heat and cause wear. Similarly, over-lubricating will require the motor to exert too much energy. To ensure continuously smooth performance, drain and replace old lubricant according to the recommended schedule. It’s also important to always use the same lubricant, as mixing products can diminish lubrication performance and in some cases cause catastrophic bearing failure.
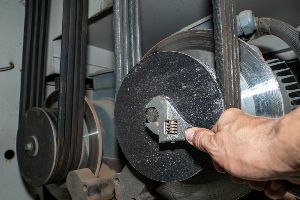
2. Reduce Motor Vibration
When motors are in motion, excess vibration can cause premature bearing wear. During motor inspections, a professional will tighten loose parts, align the motor shaft, and sustain proper belt tension to reduce vibrations. It’s also critical to keep the motor away from secondary vibrations caused by nearby equipment.
Since vibrational changes can be difficult to detect over time, technicians are encouraged to record and routinely monitor a motor’s vibrational data after it has been installed. When testing logs reveal a spike, identify and resolve the source of vibration to prevent damage.
3. Control Moisture
Although lubricant can protect bearings and other parts from corrosion, moisture can still build up when the motor is idle. Specifically, when the motor is non-operational, the change in temperature can lead to a buildup of moisture, which in turn, will cause metal components to degrade.
You can minimize moisture problems by keeping equipment in an area with stable temperatures and low humidity. Since condensation can’t be eliminated entirely, use a lubricant made with a fortified rust inhibitor formula.
Keeping bearings and other components in good condition is simple when you rely on the experts at Hayden Electric Motors. Serving Anchorage, AK since 1959, these specialists follow strict industry standards to diagnose performance issues—such as excessive vibration—and provide reliable electric motor repairs to keep equipment running strong. They also offer comprehensive electric motor maintenance services to ensure optimal equipment efficiency. For more details on their capabilities, visit this electric motor and generator repair company online. To request assistance, call (907) 561-1073.
About the Business
Have a question? Ask the experts!
Send your question