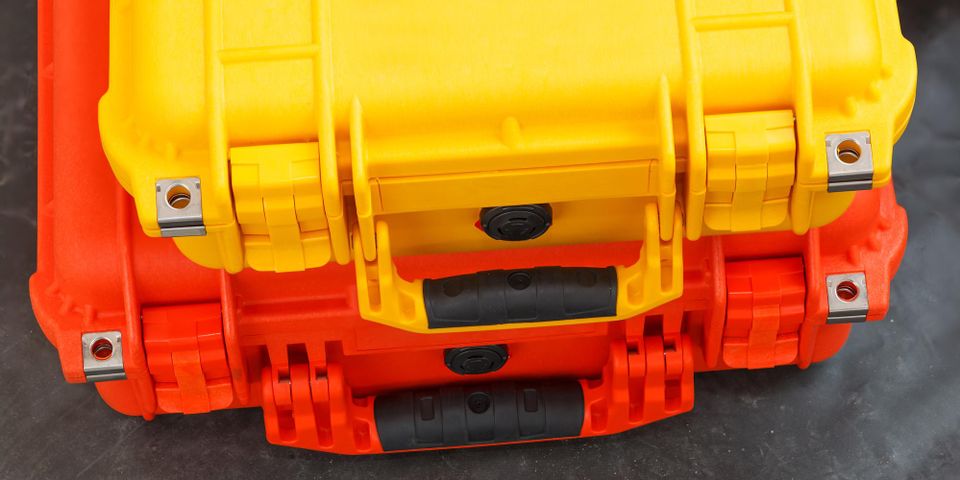
Solvent bonding is a popular technique used in custom plastic product fabrication and packaging. For many businesses, it’s a smart alternative to options such as heat sealing or RF welding. If you plan to use it, it’s common to have some questions about what’s involved in the process and why it would be the right choice for you. Below is a brief guide to the topic.
How It’s Done
Solvent bonding is a sealing process typically used in custom plastic work. The two surfaces that must be joined are cleaned to remove any contaminants. A special solution is chosen depending on the materials you want to seal and applied to the objects. This causes both surfaces to soften and dissolve. They are pressed together with pressure, and as the solvent evaporates the surfaces form entangled polymer chains to create a permanent seal. The evaporation process can take up to 24 hours. The residual substance must be removed immediately, so it will not affect the bond’s integrity. Some common solvents include methyl ethyl ketone, cyclohexanone, methylene chloride, and tetrahydrofuran.
Why It’s a Smart Choice
Solvent bonding can be used in packaging, such as sealing plastic sheets together. It can also be used to create prototypes to combine dissimilar materials or insert tubs for airtight and watertight custom plastic products. Because the process doesn’t require heat, it won’t damage any items, such as connectors or flexible plastic, that would be distorted in such a process. The strong bond formed between the two materials looks clean and is also air- and fluid-tight.
If you’re not sure whether solvent bonding is the best choice for your product, the experts at Faro Industries can help you decide. Their custom plastic and 3D printing service is based in Rochester, NY, and serves customers throughout the U.S. and overseas. They use cutting-edge technology to fulfill orders of varying sizes. Visit them online to learn more about their work, or call (585) 647-6000 to discuss your needs with a representative.
About the Business
Have a question? Ask the experts!
Send your question