What is Ultrasonic Welding?
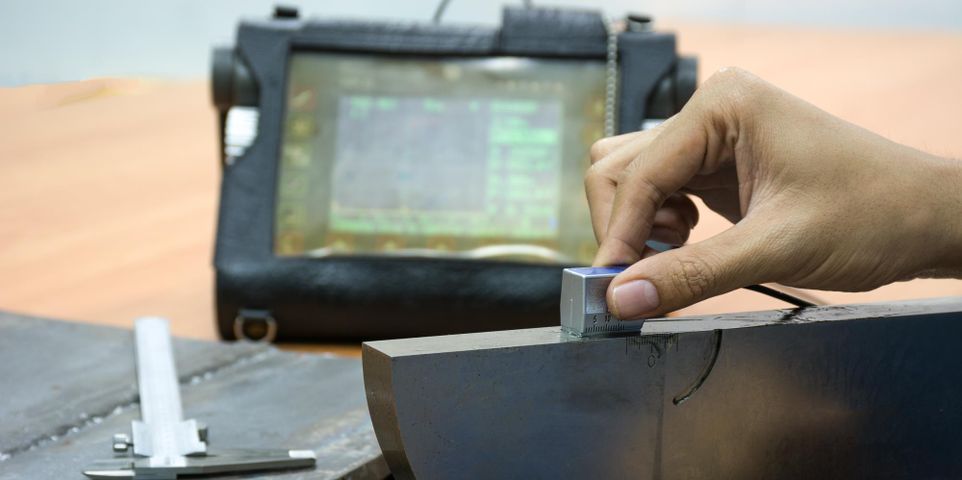
When designing prototypes or fabricating new products like retail displays, automotive trim, or medical devices, designers always need to find a way to bond individual pieces together. Ultrasonic welding is a modern way to connect plastics and other materials without using an open flame. If you’re unfamiliar with this technique and its various applications, here’s some helpful information on the process.
Understanding Ultrasonic Welding
What is this process?
Traditionally, plastics were bonded together using an open flame to melt two pieces into one. Ultrasonic welding uses high-frequency sound waves and pressure to bond two pieces of plastic together instead of using a torch. The friction creates heat, allowing two pieces of plastic to seamlessly connect. This technique is increasingly popular in the professional plastics industry as it’s the fastest way to band plastics together.
What are the Benefits of This Process?
Ultrasonic welding does not require soldering equipment or connective bolts to bond two items. Thus, manufacturing and production costs are significantly lower with this process. Additionally, ultrasonic welding can be automated for added precision with a trained welder simply preparing and monitoring the activity. Through ultrasonic welds, you won’t see visible seams. The result is often more visually appealing and smoother than a traditional welding job. This technique is prevalent in the manufacturing of electronics and circuitry since it creates a reliable bond without changing the thermal environment.
Faro Industries in Monroe County, NY, has been a global leader in custom plastic components, assembly, and welding since 1967. This team of professionals specializes in the general fabrication of products and plastic components for food containers, electronic devices, medical tools, and beyond. Call today at (585) 647-6000 to discuss your plastic needs or visit their website to read more about their work.
About the Business
Have a question? Ask the experts!
Send your question