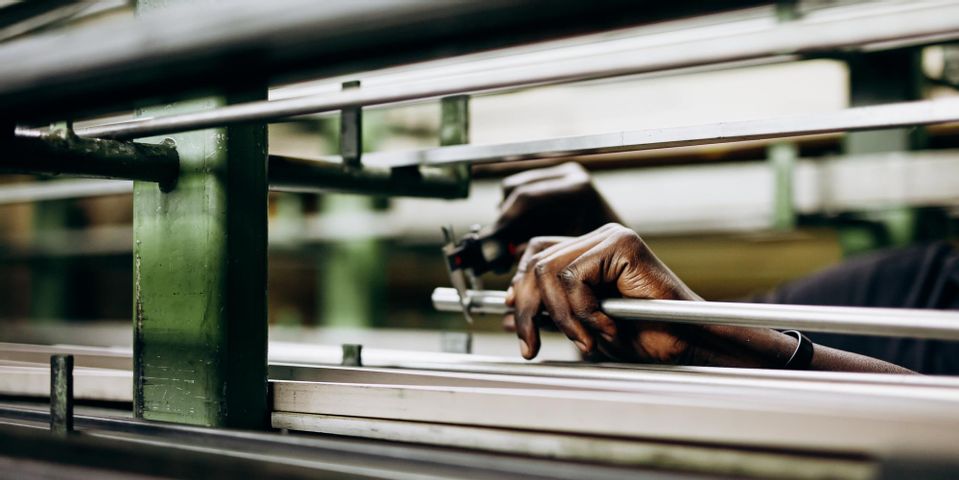
When it comes to building strong, cleverly-designed structures, aluminum extrusion plays a significant role. Even if you don’t have much experience in the metal fabrication industry, you’ll be able to understand its importance and versatility. Use the following guide to learn more about aluminum extrusion and how it might serve your project.
How Does the Process Work?
If you’ve ever pushed play dough through a mold, you’ll understand the process of aluminum extrusion. The process begins with two main components, a cylinder of aluminum alloy and a die.
First, the alloy is heated to extreme temperatures (upward of 800 degrees), and the die is properly lubricated. Then, a ram is used to shove the alloy through the die, pushing it out the other side.
The die exerts pressure on the malleable aluminum, turning it into an object with a uniform cross-sectional profile, such as a pipe. Once the metal has been elongated, or “extruded,” it is laid to rest on a table and cooled off with fans.
What Is It Used For?
Even though the aluminum is soft to start with, the finished product is stable and strong. As a result, aluminum extrusion is used for various applications in the construction and architectural industries.
Three main shapes can be formed through this process: solid beams, hollow tubes, or semi-hollow pieces (such as a closed beam with a tight gap on one side). These are essential to many aspects of building construction, from residential drainage systems and window frames to the International Space Station.
To take advantage of this metal fabrication technique yourself, reach out to International Extrusions of Garden City, MI. They have been mastering their trade for over eight decades, and they’re proud to offer both standard and custom dies for creating aluminum components. They can also add powder coatings to your metal products to enhance the strength or add color to your creations. To learn more about their offerings, visit them online or call (734) 427-8700 to request an estimate.
About the Business
Have a question? Ask the experts!
Send your question