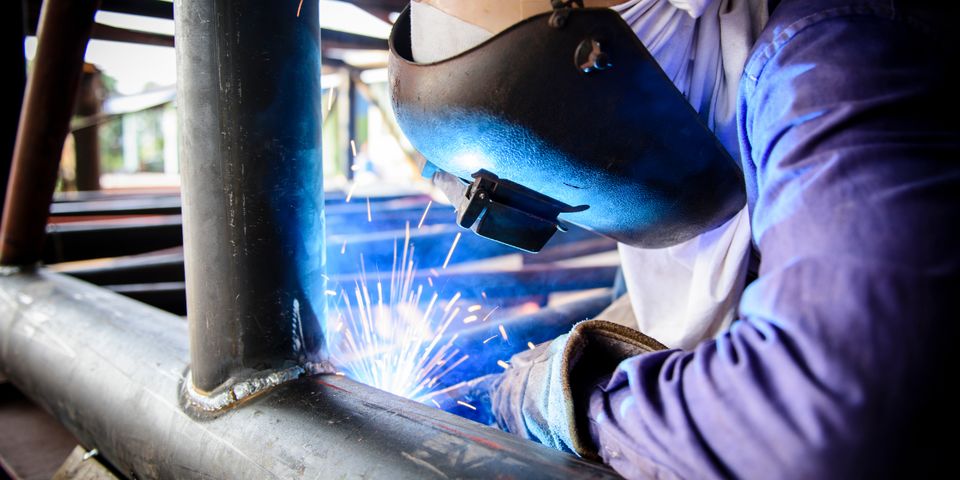
With the right tools and training, a skilled fabricator can turn raw metal stock into anything from door hinges to high-performance aircraft parts. Almost every industry relies on metal fabrication experts to create tools, product components, and replacement parts for valuable equipment. The following guide offers a brief overview of how fabricators shape metal stock to a client’s specifications.
5 Steps of the Metal Fabrication Process
1. Designing
Before work starts, fabricators create a design detailing every aspect of the product. Advanced CAD software allows a metal shop to generate 3D renders, views from multiple angles, and see how parts fit together. A thorough design minimizes the risk of mistakes and helps fabricators anticipate problems before creating the product.
2. Cutting the Metal
Depending on the thickness of the stock and the object they’re creating, metalworkers might use laser cutting, water jet cutting, or saws to shear metal. Lasers are the most accurate technique and are usually used when working with thinner metals. If the project calls for especially thick pieces or solid blocks of steel, mechanical shearing tools are generally a better choice.
3. Forming
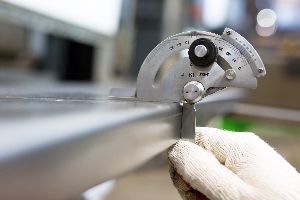
Forming is the process of shaping cut stock into the final product. Depending on the project, this step might include bending and folding, punching holes, or grinding parts into their final shape. Some projects might call for extrusion, a process in which metal is forced through an opening to create specific, complex shapes. Complex metal fabrication projects might require several advanced techniques to achieve the desired result.
4. Assembly
If the final product consists of several parts, they must be assembled and fixed together. In some cases, fabricators might use rivets or screws, but welding is the most common technique. Welding uses an electrical current to bond two metal edges at the molecular level, creating a joint that may be stronger than the rest of the part.
5. Finishing the Metal
Finishing involves treating the surface to prevent rust, reduce wear, or enhance the aesthetics of the finished piece. Depending on the type of metal and the purpose of the part, your fabricator might apply paint or powder-coating, each of which reduces corrosion. Electroplating is another common technique for creating a durable finish resistant to friction, heat, and corrosion.
No matter what project you’re planning, you can rely on International Extrusions in Garden City, MI, for reliable quality and exceptional service. In addition to expert CNC fabrication, they’re also a national leader in aluminum extrusion technology, delivering highly accurate parts to companies across the country. Visit their website to learn more about their fabrication services, get more professional insight on Facebook, or call (734) 427-8700 to discuss your project with a member of their team.
About the Business
Have a question? Ask the experts!
Send your question